What Type Of Tech Skills Does a Welder Need: A Comprehensive Guide to Thriving in the Welding Industry
What Is Welding Manufacturing businesses along with construction and automotive operations use welding as their basic foundation. Welding technology establishes...
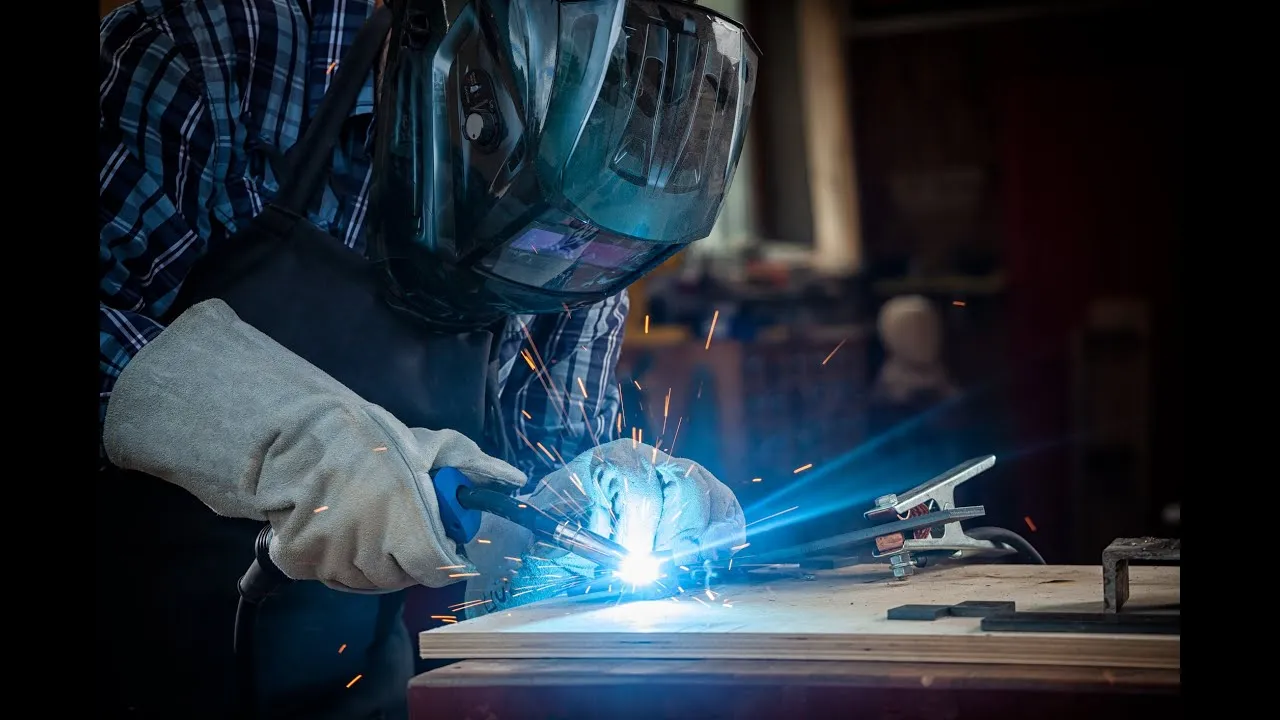
What Is Welding
Manufacturing businesses along with construction and automotive operations use welding as their basic foundation. Welding technology establishes the basis for building the essential structures and items we depend on today. Technology advancements together with industry standard progress require welders to master multiple specialized skill sets for superior performance. Professionals who want to succeed in 2025 need fundamental welding skills as an essential requirement to pursue lasting success and develop their careers. You can learn more by watching this Short YouTube Video.
The guide provides complete information about welding fundamentals alongside training essentials and occupational responsibilities alongside advanced competencies and future welding industry predictions.
I. Foundational Welding Skills
Understanding Welding Equipment and Tools
The initial requirement for skilled welding starts by grasping welding equipment fundamentals. Welders operate with welding machines, torches, grinders and personal protective equipment (PPE) through their daily work practice. A working knowledge of maintenance procedures combined with machine operation and troubleshooting capacities leads to safe and productive job execution.
Overview of Tools: To become a welder one needs to understand MIG machines along with TIG machines and Stick welders. Complete mastery of welding requires a full understanding of basic tools including clamps, welding rods and shielding gases.
Maintenance and Troubleshooting: Equipment failure prevention depends on scheduled equipment maintenance which includes both checking for wear and systematic cleaning procedures. The mastery of simple troubleshooting tools allows workers to decrease equipment breakdown and maintain project timelines.
Mastering Safety Protocols
Safety is paramount in welding. Welders undergoing work without protective measures become at risk for suffering burns and electric shocks and breathing dangerous fumes.
Importance of Workplace Safety: Safety guideline compliance protects both personnel welfare and safeguards industry regulatory standards.
Common Hazards: Welders need to detect hazards consisting of ultraviolet radiation along with high heat and fire dangers. Workers who follow the recommended procedures for PPE use including wearing gloves alongside helmets with built-in lenses and fire-safe apparel minimize most dangers in their workspace.
Welding Techniques
Multiple welding techniques create fundamental requirements for successful job execution across different welding tasks.
Key Techniques: The mastery of MIG (Metal Inert Gas), TIG (Tungsten Inert Gas), and the stick welding method should be acquired by all welders. Each technique has specific applications and benefits:
MIG: Ideal for high-speed projects and thicker materials.
TIG: Clean welds together with precise results make this technique optimal for thin materials.
Stick Welding: Versatile and effective for outdoor or adverse conditions.
Choosing the Right Technique: Technique selection relies on material nature alongside project demands along with requested surface appearance.
II. Importance of Welder Training Programs
Hands-On Training
Welders require practical experience because it holds essential value in their profession. Welder training programs along with apprenticeship programs let participants develop their skills through supervised work practice.
Value of Practical Experience: Welding practitioners learn how to turn classroom principles into practical results through physical practice. When welders work across different projects they build their practical abilities and self-assurance simultaneously.
Examples of Top Programs: Welders who obtain certifications from recognized programs including the American Welding Society (AWS) or neighborhood trade schools develop both stronger professional standing and increased career opportunities.
Certifications and Credentials
Welding professionals must gain certifications which serve as fundamental requirements for progressing their careers.
Key Certifications: To advance their career welders should acquire AWS Certified Welder as well as ASME Boiler and Pressure Vessel Code Certification together with specialized endorsements specific to pipe welding and structural steel welding.
Benefits of Certification: Workers who possess welding certifications achieve both better professional market success along with increased wage potential while obtaining niche positions in their field.
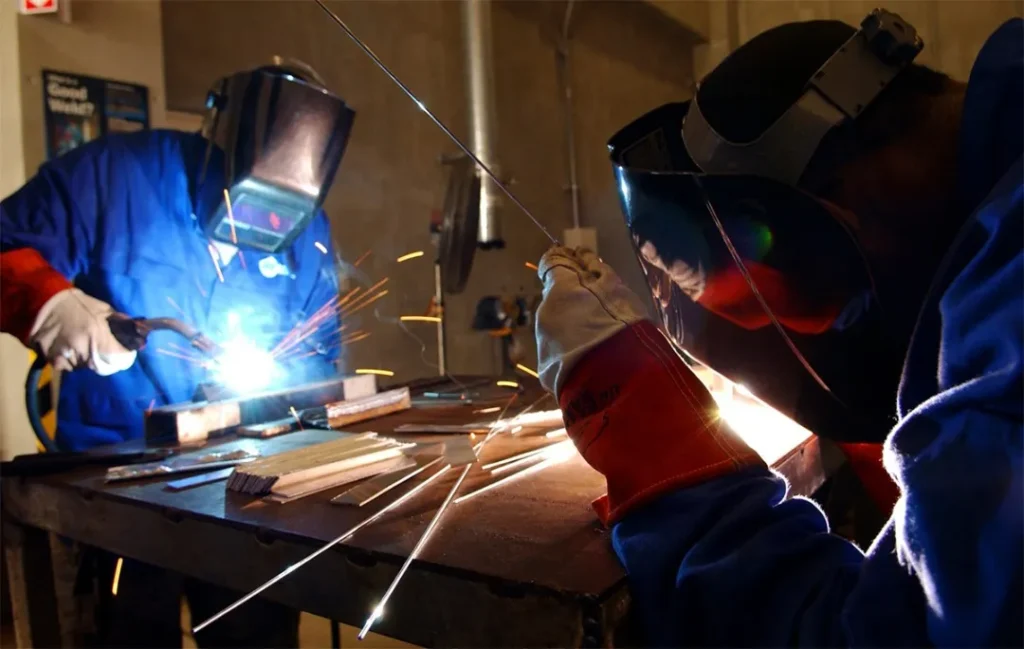
III. Job Duties and Responsibilities of Welders
Day-to-Day Tasks
Professional welders perform multiple daily tasks requiring both high levels of precision along with detailed work habits.
Preparing Materials: They measure materials and perform steel sectioning before placing metals components based on project requirements.
Reading Blueprints: Technical drawings require interpretation before welders can achieve project accuracy.
Setting Up Equipment: The proper setup of welding machines together with tools serves as a fundamental requirement for achieving work efficiency.
Performing Quality Control: Weld examination of completed work verifies both safety requirements and structural protocols.
Project-Based Responsibilities
Welders work alongside engineers and both contractors and other professionals during the execution of major construction projects.
Coordination with Teams: The combination of effective communication together with team coordination enables project groups to finish their work both on schedule and within the planned budget.
Meeting Deadlines: Speed and quality work hand in hand for essential processes especially when industry delays result in significant expenses.
IV. Specialized Welding Skills for Career Growth
Blueprint Reading and Interpretation
The mastery of technical skills produces superior efficiency while assuring precise work output.
Importance of Blueprint Reading: Accurate blueprint interpretation by welders enables them to meet exact project requirements.
Enhancing Project Accuracy: Technical drawings become clearer when understood because this minimizes mistakes and waste reduction happens simultaneously.
Knowledge of Metallurgy and Materials
Welders who possess a complete understanding of metallurgy can work successfully on different types of metal.
Understanding Metal Properties: Workers who perform welds need to understand how different materials behave when heat affects them and when under pressure while being welded.
Applications in Advanced Techniques: Professional mettalurgical knowledge serves critical welding functions including the repair of rare metals and operations in demanding high-pressure conditions.
Soft Skills
A welder requires both technical expertise together with soft skills for their professional success.
Problem-Solving: Welders frequently encounter unexpected obstacles because materials exhibit deviation from expected results and equipment demonstrates unpredictable breakdowns.
Teamwork: When welders work alongside their colleagues they create a foundation for project success.
Communication Skills: Quality interaction between welders and their clients along with their supervisors develops trust relationships while maintaining shared comprehension.
V. Future Trends in Welding
Technological Advancements
Active changes in welding technology currently define industry development by changing welder approaches across the field.
Robotics and Automation: Technology advances keep bringing robots into repetitive hazardous duties so welders can handle complex tasks. Welders who learn to work with automated systems continue to find high levels of job demand.
Digital Tools: Welding machines featuring advanced technologies with real-time monitoring systems alongside precise tool control software are shifting from custom machines to standard industry tools.
Sustainability Practices
Managing sustainability has become essential for industries which drives the adoption of environmentally friendly welding practices into the spotlight.
Eco-Friendly Techniques: Two welding methods called cold welding and friction stir welding help minimize energy consumption during operations.
Recycling and Waste Management: The practice of reusing raw materials together with waste reduction allows welders to advance sustainability goals.
Read More : Can You Get Your Vehicle Fixed At a Vo-Tech School?
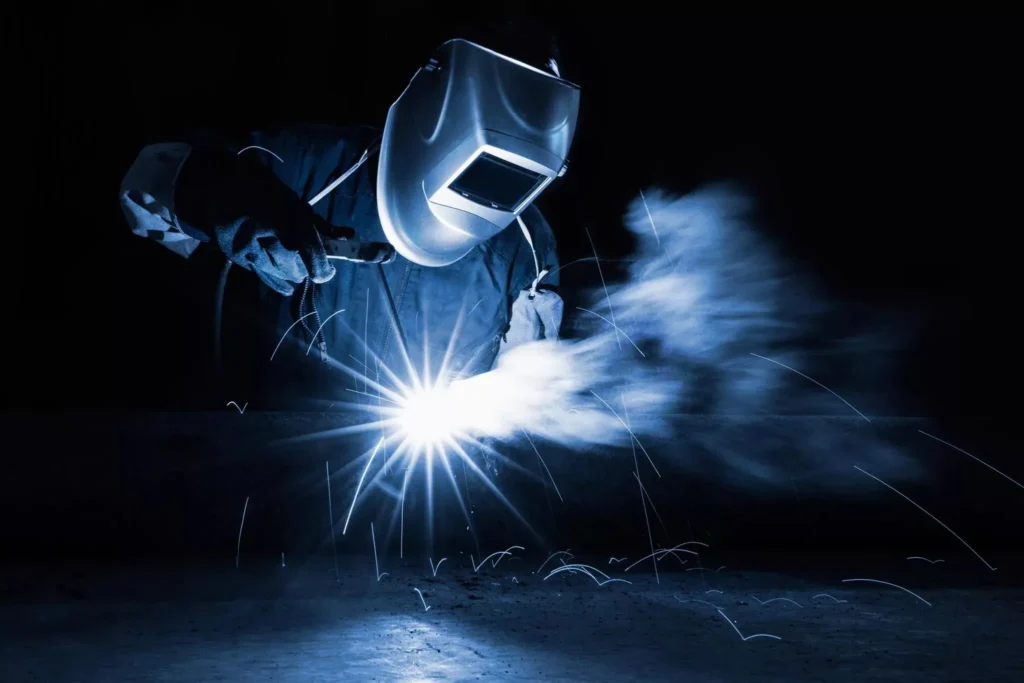
Conclusion
In order to succeed in the welding industry of 2025 and beyond, welders require mastery of essential core competencies. Welders need to develop three fundamental sets of abilities starting with basic safety skills and welding fundamentals along with specialized knowledge in metallurgy along with blueprint interpretation abilities to fulfill current industry needs. Belonging to professional scrutiny organizations combined with field-specific hands-on learning experiences along with continuous learning habits keeps professionals competitive within this active field of work.
The welding industry is changing through technological advances and sustainability demands so individuals who combine these shifts with career development will lead the profession’s vital work. Building a successful welding career requires skill development along with the capability to change course within an industry which constantly evolves.