The Importance of Precision in Chemical Blending for Quality Products
Chemical blending plays a vital role in various industries, from pharmaceuticals and cosmetics to food production and industrial manufacturing. Achieving...
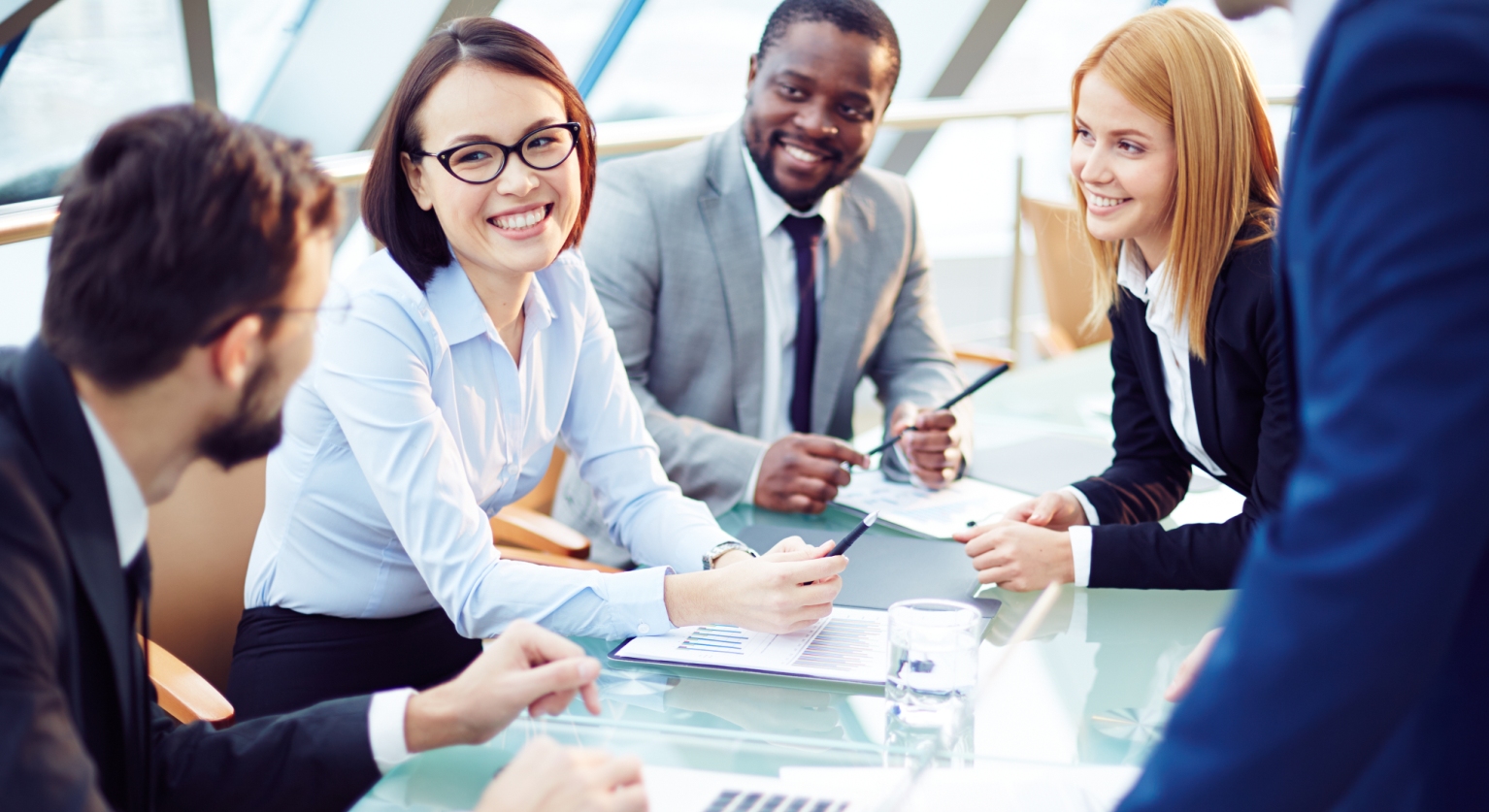
Chemical blending plays a vital role in various industries, from pharmaceuticals and cosmetics to food production and industrial manufacturing. Achieving the right balance of ingredients is crucial to ensuring product quality, safety, and effectiveness. Even the slightest deviation in measurements or mixing procedures can result in ineffective or even hazardous final products. This article explores the significance of precision in chemical blending, common challenges, and best practices to maintain quality standards.
What Is Chemical Blending?
Chemical blending is the process of combining different chemical substances to create a final product with specific properties. This can involve mixing liquids, solids, or gases in precise ratios to achieve the desired chemical reaction or formulation. The process is widely used in industries such as:
- Pharmaceuticals: For producing medicines, vaccines, and healthcare products.
- Cosmetics: In formulating skincare, haircare, and personal care products.
- Food and Beverages: To ensure the correct balance of ingredients in processed foods, flavorings, and preservatives.
- Industrial Applications: For manufacturing paints, adhesives, lubricants, and cleaning agents.
Why Is Precision Important in Chemical Blending?
Precision is crucial in chemical blending because even a minor miscalculation can alter the final product’s performance, consistency, and safety. Here’s why accuracy matters:
- Consistency in Quality
Industries rely on chemical blending to produce products that perform the same way every time. For example, a pharmaceutical company must ensure that every batch of medication contains the exact same concentration of active ingredients to guarantee effectiveness. - Safety Concerns
Incorrect blending can result in harmful chemical reactions, leading to toxic byproducts, flammability, or even explosions. In food production, inaccurate blending could introduce allergens or unsafe chemical levels. - Regulatory Compliance
Many industries must comply with strict government regulations to ensure safety and efficacy. Regulatory bodies like the FDA, EPA, and OSHA impose guidelines that companies must follow to maintain compliance. - Cost Efficiency
Precise chemical blending helps manufacturers avoid material waste and costly reworks. Errors in formulation can lead to defective batches, which must be discarded, leading to financial losses. - Environmental Responsibility
Overuse of certain chemicals due to inaccurate blending can increase waste and environmental pollution. By maintaining precise measurements, companies can reduce their environmental footprint.
What Are the Challenges in Chemical Blending?
Achieving precision in chemical blending is not always easy. Several challenges can arise, including:
- Variability in Raw Materials: The quality of raw materials can differ from batch to batch, affecting the final blend.
- Human Errors: Mistakes in measurement, incorrect ingredient sequencing, or improper mixing techniques can lead to faulty products.
- Equipment Limitations: Outdated or poorly calibrated machinery may fail to achieve the required precision.
- Temperature and Humidity Effects: Environmental factors can impact chemical reactions and blending efficiency.
- Regulatory Changes: Industries must continually adapt to evolving compliance requirements, which may affect formulation processes.
How Can You Ensure Accuracy in Chemical Blending?
To achieve precision in chemical blending, companies must adopt best practices that minimize errors and maximize quality control. Some effective strategies include:
1. Use Advanced Measuring Equipment
Modern technology, such as automated weighing systems and digital flow meters, helps achieve accurate measurements, reducing the risk of human errors.
2. Implement Standard Operating Procedures (SOPs)
Standardized procedures ensure that all batches follow the same blending methods. Training employees on SOPs helps maintain consistency and prevent mistakes.
3. Conduct Regular Quality Testing
Performing quality control tests at multiple stages of production ensures that the final product meets industry standards. Analytical testing, pH checks, and viscosity measurements help verify the accuracy of the blend.
4. Maintain Equipment and Calibration
Regular maintenance of blending equipment, such as mixers, pumps, and dispensers, is essential to prevent malfunctions that could compromise accuracy.
5. Monitor Environmental Conditions
Controlling temperature, humidity, and pressure in production facilities can prevent variations that affect chemical blending outcomes.
6. Ensure Supplier Consistency
Using high-quality raw materials from reliable suppliers minimizes variations in ingredient properties, leading to more consistent blends.
What Industries Rely on Chemical Blending the Most?
Many industries depend on precise chemical blending to maintain the integrity of their products. Some of the most prominent sectors include:
- Pharmaceuticals: Ensuring the right mix of active and inactive ingredients for medicines and supplements.
- Cosmetics & Personal Care: Creating safe and effective skincare, makeup, and hygiene products.
- Food & Beverage: Blending flavors, preservatives, and additives for consistent taste and quality.
- Agriculture: Formulating fertilizers, pesticides, and herbicides for effective crop protection.
- Automotive & Manufacturing: Producing lubricants, adhesives, and coatings that enhance product performance.
How Does Chemical Blending Impact Product Longevity?
The accuracy of chemical blending directly affects a product’s shelf life. If a formulation is not correctly balanced, it may degrade faster or become ineffective over time. For example:
- A skincare product with an incorrect preservative ratio may spoil quickly.
- A medication with uneven active ingredient distribution may lose potency.
- A paint mixture with imprecise blending can separate or harden before use.
Properly blended chemicals ensure that products remain effective throughout their intended shelf life, reducing waste and enhancing customer satisfaction.
What Are the Future Trends in Chemical Blending?
Advancements in technology and sustainability practices are shaping the future of chemical blending. Some emerging trends include:
- Automation and AI Integration: The use of robotics and artificial intelligence in chemical blending enhances precision and reduces human errors.
- Eco-Friendly Formulations: Many industries are shifting towards sustainable, biodegradable, and non-toxic chemical blends.
- Improved Quality Control Systems: Enhanced data tracking and real-time monitoring are making it easier to maintain high standards.
- Customized Blending Solutions: Businesses are investing in specialized blending services to create tailored formulations for unique applications.
Conclusion
Precision in chemical blending is essential for ensuring product quality, safety, and consistency across various industries. Companies that prioritize accurate measurements, advanced technology, and strict quality control measures can minimize risks and maximize efficiency. As industries continue to evolve, adopting modern blending techniques and sustainable practices will be key to maintaining high standards and meeting consumer expectations.
By understanding the importance of precision in chemical blending, businesses can create reliable products that meet regulatory standards while optimizing costs and environmental impact.