Shell and Tube Heat Exchangers: The Engineered Backbone of Thermal Systems
Shell and tube warmth exchangers are among the maximum widely used and reliable devices in business thermal control. Their robust...
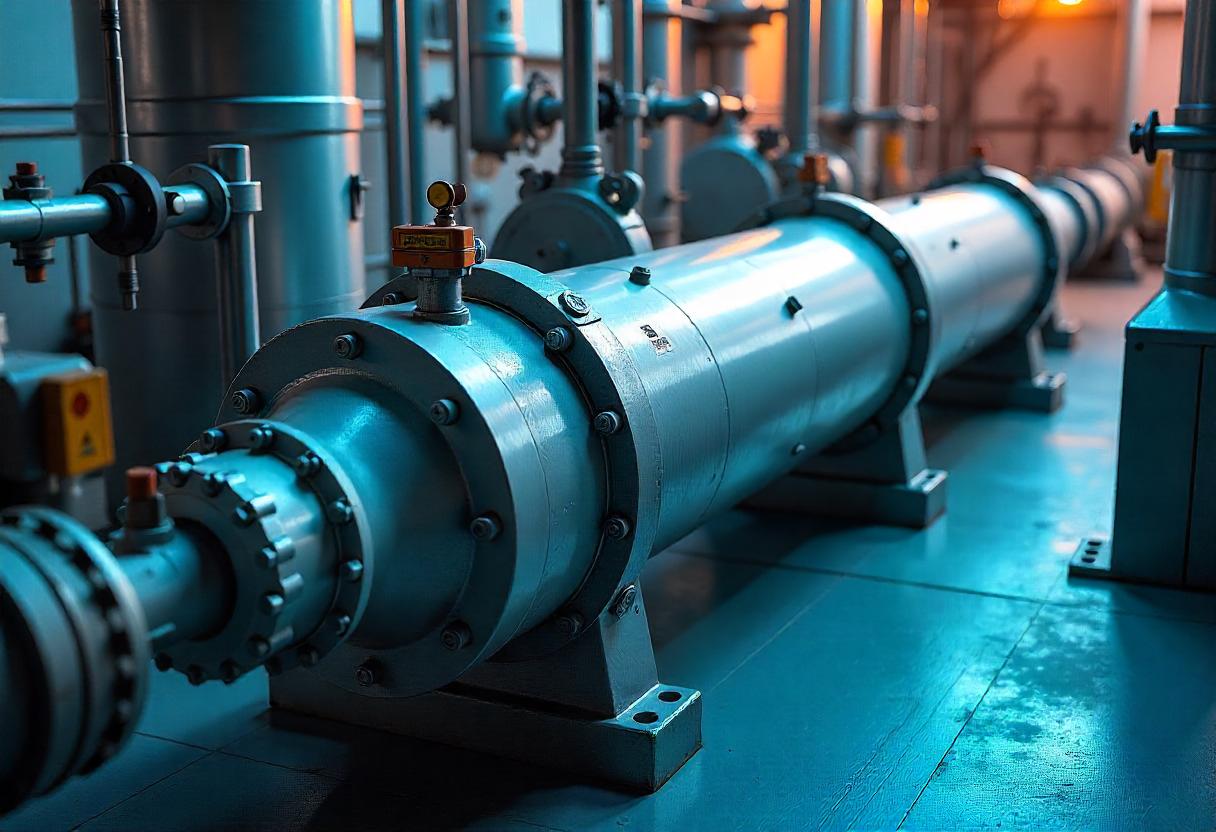
Shell and tube warmth exchangers are among the maximum widely used and reliable devices in business thermal control. Their robust layout, adaptability to excessive pressures and temperatures, and ease of upkeep have made them a cornerstone in sectors ranging from power technology to chemical processing. These exchangers consist of a cylindrical shell containing a package deal of tubes via which fluids flow to switch warmness among two media without blending. This fundamental design precept helps a vast range of packages and guarantees long-time period operational reliability.
Industries depend on shell and tube heat exchangers for each heating and cooling procedures, facilitating electricity-green operations in refineries, petrochemical plants, food processing units, and extra. Their established overall performance and versatility allow engineers to tailor configurations according to technique specs. The role of a skilled business merchandise manufacturer is important in ensuring those systems are built to exacting standards and optimized for performance under particular running conditions.
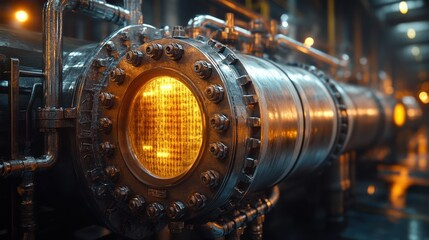
How Shell and Tube Heat Exchangers Work
At the coronary heart of a shell and tube heat exchanger is a easy however powerful design that separates the two fluids even as allowing thermal strength to pass among them. One fluid flows thru the tubes while the alternative circulates round them in the shell. The warmth switch happens through the tube walls, which are made of conductive materials to facilitate efficient strength exchange.
These exchangers may be configured in unmarried-skip or multi-bypass designs relying at the desired thermal output. In single-pass designs, the fluid flows in a single direction thru the tubes, while multi-skip designs permit the fluid to opposite route to decorate warmness switch efficiency. The configuration and waft preparations—whether or not parallel flow, counterflow, or crossflow—impact the overall effectiveness and are selected primarily based on software requirements.
Thermal conductivity, pressure drop, and fouling resistance are key performance criteria. The preference of materials, wide variety of tubes, baffle preparations, and shell diameter all contribute to the exchanger’s capability to satisfy excessive heat obligation demands in a compact and maintainable form.
Applications Across Diverse Industries
The vast use of shell and tube warmth exchangers is pushed by means of their ability to handle loads of fluids and operating situations. In the oil and gas industry, they are used to condense vapors, preheat crude oil, or quiet down refined products. Their resistance to high pressures and capacity to control thermal expansion make them appropriate for heavy-responsibility applications along with steam generation and manner heating.
In energy flowers, these exchangers are generally used to recover waste heat from turbine exhaust gases or to preheat boiler feedwater, improving typical plant efficiency. Their reliability is critical in keeping solid operation beneath fluctuating load conditions.
The meals and beverage zone benefits from their use in pasteurization, sterilization, and cooling tactics, where sanitary designs and particular temperature control are vital. Similarly, within the pharmaceutical industry, shell and tube warmness exchangers guide sterile environments and consistent thermal performance in sensitive drug manufacturing tactics.
In HVAC structures and district cooling networks, those heat exchangers play a essential function in dealing with building temperatures, lowering strength consumption, and enhancing occupant consolation.
Design Configurations and Customization
The flexibility in shell and tube warmness exchanger layout permits for tremendous customization. Depending on the particular application, engineers can adjust elements along with tube diameter, tube pitch, baffle spacing, and go with the flow arrangement. These layout variables have an effect on warmth transfer efficiency, stress drop, and susceptibility to fouling.
A commonplace configuration entails U-tube designs, in which one quit of the tube package deal is fixed whilst the other quit is loose to extend and agreement. This design incorporates thermal enlargement and is good for programs involving big temperature variations. Straight tube designs, alternatively, are less complicated to clean and inspect, making them suitable for services where preservation get entry to is a priority.
Baffles within the shell direct the shell-facet fluid drift across the tubes multiple times, increasing turbulence and improving warmness transfer. However, baffle layout ought to stability heat switch profits with pressure drop boundaries to make certain strength-efficient operation.
Material choice is another vital issue. Depending on fluid residences, corrosion resistance, and temperature requirements, materials like chrome steel, titanium, copper alloys, or carbon metal may be used. The compatibility of those substances with the fluids guarantees lengthy service lifestyles and prevents problems like erosion or scaling.
Efficiency and Maintenance Considerations
While shell and tube heat exchangers are known for their excessive warmness transfer charges and sturdiness, their long-time period performance depends on proper operation and preservation. One of the number one concerns is fouling, which occurs when deposits form at the tube surfaces, lowering warmth transfer performance and increasing stress drop. This trouble is particularly widely wide-spread in structures handling impure or scaling-susceptible fluids.
Routine inspection and cleansing are important for sustaining overall performance. Removable tube bundles and available shell-side additives make upkeep possible, specially in industries in which equipment downtime directly influences productivity. Techniques like chemical cleaning, mechanical brushing, and high-stress water jetting are commonly hired to restore overall performance.
Monitoring parameters like pressure drop, temperature differentials, and fluid excellent can assist hit upon early signs and symptoms of fouling or mechanical put on. When incorporated into predictive preservation applications, these indicators help in scheduling timely interventions and stopping pricey disasters.
Efficient operation also hinges on right installation and integration in the broader thermal system. Positioning, glide balancing, and insulation all make contributions to minimizing energy loss and maximizing output. A well-included shell and tube warmness exchanger machine frequently yields decreased power prices and stepped forward thermal stability throughout the procedure.
Energy Conservation and Environmental Benefits
With the developing emphasis on sustainability, shell and tube warmness exchangers have taken on a greater outstanding role in power conservation strategies. Their potential to recover heat from exhaust streams or recycle thermal electricity within a method facilitates lessen gasoline consumption and decrease greenhouse gasoline emissions.
In wastewater remedy flowers, these exchangers can preheat incoming water the usage of heat recovered from effluent streams, decreasing the energy required for treatment. Similarly, in industrial dryers and incinerators, they seize residual warmth for reuse in preheating combustion air or producing steam.
By integrating shell and tube warmth exchangers into closed-loop systems, industries can create extra self-maintaining operations. These structures not most effective keep on electricity expenses but also contribute to a decrease environmental footprint, aligning with regulatory requirements and corporate sustainability goals.
The guide of a succesful business products manufacturer is vital when designing for energy healing, as those experts ensure the gadget meets overall performance expectations whilst staying within environmental and operational limits.
Advances in Computational Design and Manufacturing
Modern shell and tube heat exchangers benefit from advances in computational fluid dynamics (CFD), finite element analysis (FEA), and automated fabrication strategies. These gear enable engineers to model complex glide behaviors, optimize warmness switch surfaces, and reduce pressure drop—all before bodily prototypes are constructed.
Simulation-pushed layout reduces improvement time and increases accuracy, specially for custom-built exchangers in particular business settings. Engineers can take a look at more than one scenarios and configurations digitally, predicting overall performance effects beneath diverse conditions.
On the manufacturing aspect, precision machining and welding technology improve creation great, while modular designs make meeting and destiny improvements less complicated. Enhanced inspection techniques, which includes radiographic and ultrasonic trying out, make certain structural integrity and compliance with industry requirements.
Together, those innovations permit shell and tube warmness exchangers to fulfill evolving commercial demands while preserving first-rate reliability, even inside the most hard environments.
Safety and Regulatory Compliance
Industrial warmth alternate systems must meet rigorous safety and regulatory requirements to save you injuries, leaks, and disasters. Shell and tube warmness exchangers are designed according with standards which includes ASME, TEMA, and ISO, which provide tips for stress vessel integrity, thermal performance, and cloth specs.
Safety features include pressure remedy valves, rupture discs, and corrosion allowances constructed into the design. Proper fabrication practices, licensed welders, and thorough inspections are obligatory to make sure these systems function adequately beneath excessive pressures and temperatures.
Failure to conform with those standards can bring about operational hazards, fines, or device breakdowns. Therefore, industries have to collaborate with skilled engineers and manufacturers who understand the regulatory landscape and may deliver licensed device suitable for vital packages.
The Future of Thermal Management with Shell and Tube Designs
Looking beforehand, the continuing importance of shell and tube warmness exchangers within the face of world energy and environmental demanding situations cannot be overstated. As industries attempt for carbon neutrality and useful resource efficiency, these exchangers are poised to play an even more substantial role in sustainable manner engineering.
Emerging materials, such as composite metals and nanocoatings, promise to improve thermal performance and fouling resistance. Additionally, integration with virtual monitoring systems and clever procedure control will enhance real-time overall performance tracking, making thermal systems extra shrewd and adaptive.
In mixture with renewable electricity systems, inclusive of solar thermal collectors and geothermal vegetation, shell and tube warmth exchangers can serve as bridges between traditional and sustainable technologies. Their proven song file, combined with ongoing innovation, ensures they remain at the vanguard of industrial warmth switch answers.
Conclusion: A Proven Technology for a High-Performance Future
Shell and tube heat exchangers have mounted themselves as a foundational component of thermal control in infinite industries. Their adaptability, efficiency, and sturdiness cause them to critical in complex systems requiring unique temperature control and strength conservation.
Whether helping important features in a refinery or dealing with technique heat in a pharmaceutical facility, these exchangers supply constant performance over long service lives. As industries evolve toward more sustainable and sensible operations, shell and tube heat exchangers will preserve to offer reliable solutions that meet both performance dreams and environmental duties.
With the guidance and aid of a professional industrial product manufacturer, organizations can fully leverage the capabilities of these systems to obtain operational excellence, strength efficiency, and lengthy-term fee.