Reinventing Metal Fabrication: A Deep Dive into Wire Arc Additive Manufacturing (WAAM)
In the rapidly evolving world of manufacturing, additive processes have transformed how we think about design, prototyping, and production. While...
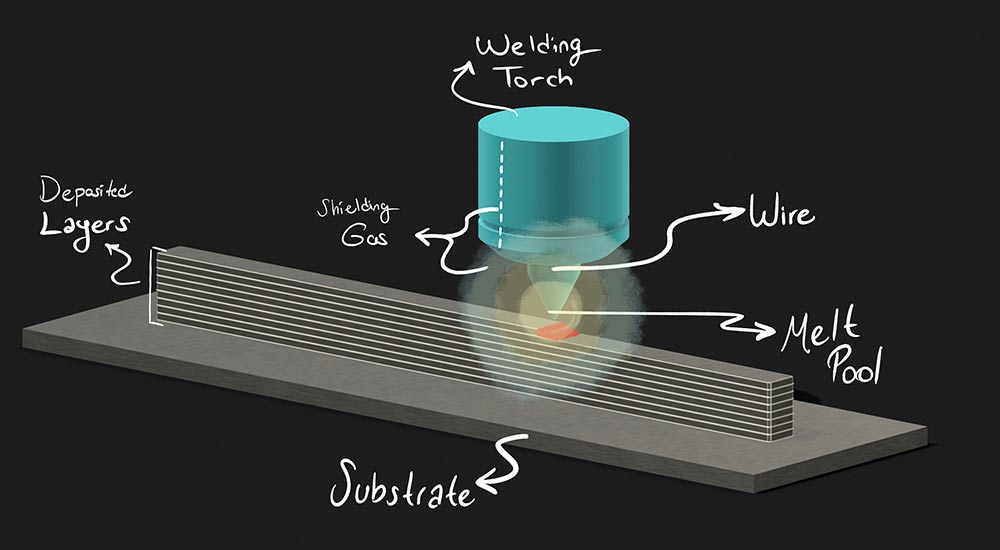
In the rapidly evolving world of manufacturing, additive processes have transformed how we think about design, prototyping, and production. While plastic 3D printing has become mainstream, metal additive manufacturing is the frontier that’s reshaping industries like aerospace, automotive, marine, and defense.
Among various techniques, Wire Arc Additive Manufacturing stands out as a powerful, cost-effective solution for producing large-scale metal components with minimal material waste. Combining the principles of welding and 3D printing, WAAM offers manufacturers a way to build near-net-shape metal parts layer by layer using wire feedstock and arc welding.
In this article, we explore what WAAM is, how it works, its benefits and challenges, and the industries it’s transforming.
What Is Wire Arc Additive Manufacturing?
Wire Arc Additive Manufacturing (WAAM) is a type of Directed Energy Deposition (DED) additive manufacturing process. It uses an electric arc as the heat source and metal wire as feedstock, which is melted and deposited layer by layer to form complex metal parts.
Unlike powder-bed metal 3D printing, WAAM is more suitable for large-scale parts and structural applications. It’s built upon existing welding technologies like Gas Metal Arc Welding (GMAW), Gas Tungsten Arc Welding (GTAW), and Plasma Arc Welding (PAW), making it accessible and cost-effective for many industries.
WAAM is especially appealing because it blends traditional metalworking techniques with digital manufacturing innovations.
How Does WAAM Work?
At its core, WAAM combines robotic control, CAD modeling, and arc welding. Here’s how the process typically works:
- CAD Model Creation
The design begins in a 3D modeling software where a part is digitally created. - Slicing and Toolpath Generation
The CAD model is sliced into layers, and a toolpath is generated for the deposition head (usually a welding torch). - Wire Feeding and Arc Activation
A metal wire—commonly steel, aluminum, or titanium—is continuously fed into the arc. The arc melts the wire, and the molten metal is deposited in layers. - Layer-by-Layer Building
Controlled by robotic arms or CNC machines, the system builds up the part in successive layers, following the toolpath. - Post-Processing
After printing, parts often undergo machining, heat treatment, or inspection to ensure dimensional accuracy and mechanical performance.
Key Components of a WAAM Setup
To understand WAAM fully, it helps to know the essential components of the system:
- Welding Power Source – Provides the energy needed to melt the wire feedstock.
- Wire Feed System – Feeds the metal wire at a controlled rate to the arc.
- Robotic Arm or CNC Gantry – Positions the welding torch along the pre-defined path.
- Shielding Gas Supply – Protects the molten pool from oxidation (commonly Argon or a mix).
- Monitoring and Sensors – Cameras, thermal sensors, and control software ensure quality and consistency.
Advantages of Wire Arc Additive Manufacturing
WAAM has quickly gained traction due to several standout benefits:
🔹 Cost-Effective for Large Parts
WAAM doesn’t rely on expensive metal powders. Wire feedstock is more affordable, easier to store, and safer to handle.
🔹 High Deposition Rates
WAAM can deposit material at rates exceeding 3–5 kg/hour, making it one of the fastest metal additive processes—ideal for large components.
🔹 Material Efficiency
Since the process is additive, waste is significantly reduced compared to subtractive methods like CNC machining.
🔹 Design Flexibility
Designers can produce near-net-shape geometries that would be difficult or impossible to manufacture using traditional casting or forging.
🔹 Repair and Refurbishment
WAAM can be used to repair damaged parts or add material to worn components, extending product life.
Common Materials Used in WAAM
WAAM supports a variety of industrial-grade metals, including:
- Stainless Steels – Excellent for structural and marine applications.
- Titanium Alloys (e.g., Ti6Al4V) – Popular in aerospace and medical industries for their strength-to-weight ratio.
- Aluminum Alloys – Lightweight and corrosion-resistant.
- Nickel-Based Alloys – Suitable for high-temperature and corrosion-resistant environments.
- Mild and Carbon Steels – Cost-effective and widely available.
The selection of material depends on the application requirements such as strength, thermal resistance, corrosion resistance, and machinability.
Industrial Applications of WAAM
WAAM is transforming how industries approach manufacturing and repair:
🛩 Aerospace
Airbus, Boeing, and other aerospace giants use WAAM to build structural components like brackets, bulkheads, and ribs—reducing lead time and waste.
🛳 Marine and Shipbuilding
Large metal structures such as propeller blades, hull components, and deck structures are ideal candidates due to WAAM’s large build capacity.
🚀 Space
WAAM enables rapid production of space-worthy components using titanium and nickel alloys—at a fraction of the cost of traditional manufacturing.
🚛 Automotive
Concept cars and heavy-duty vehicles benefit from WAAM’s ability to quickly produce functional prototypes or customized parts.
🏭 Oil & Gas / Energy
WAAM is used for manufacturing and repairing critical parts like turbine blades, pipelines, and valve components.
Limitations and Challenges
Despite its advantages, WAAM has some technical and operational challenges:
🔸 Surface Finish and Accuracy
WAAM parts often require post-processing (e.g., CNC milling) to achieve the desired surface finish and dimensional tolerances.
🔸 Residual Stress and Distortion
The high heat input can cause internal stress, warping, or cracks if not managed properly.
🔸 Process Control
Maintaining consistent deposition and bead quality requires precise control of process parameters like arc stability, wire feed rate, and torch speed.
🔸 Limited Geometrical Complexity
WAAM excels at large, simple geometries. Fine or intricate features may require hybrid manufacturing or additional processing.
WAAM vs. Other Metal Additive Manufacturing Methods
Feature | WAAM | Powder Bed Fusion | Binder Jetting |
---|---|---|---|
Build Volume | Large | Medium | Large |
Material | Wire | Powder | Powder |
Deposition Rate | High | Low-Medium | Medium |
Cost | Low (per kg) | High | Medium |
Surface Finish | Rough | Fine | Moderate |
Post-Processing | Usually required | Sometimes required | Often required |
WAAM is not intended to replace all metal AM methods but serves as a complementary tool, particularly where large, strong, and simple metal parts are required.
The Future of WAAM
With ongoing research and development, WAAM is expected to become even more capable:
- Multi-material deposition for functionally graded parts
- Real-time monitoring and AI-based control systems
- Hybrid manufacturing setups (additive + subtractive in one machine)
- Automated quality assurance through integrated sensors and software
As digital manufacturing evolves, WAAM is well-positioned to play a critical role in sustainable, on-demand, large-scale metal production.
Conclusion: A Practical Revolution in Metal Manufacturing
Wire Arc Additive Manufacturing offers a powerful mix of affordability, speed, and material versatility. It provides industries with a tool that bridges the gap between prototyping and production, enabling fast and flexible fabrication of complex metal parts—especially when size and strength matter most.
From aerospace to shipbuilding, WAAM is opening new doors for innovation, repair, and custom manufacturing. As technology and automation improve, its role in shaping the future of industrial production will only grow stronger.