Precision Torque Wrench Calibration Services for Industrial Reliability
When it comes to industrial operations, precision is everything. Whether you’re working in automotive manufacturing, aerospace engineering, or heavy machinery,...
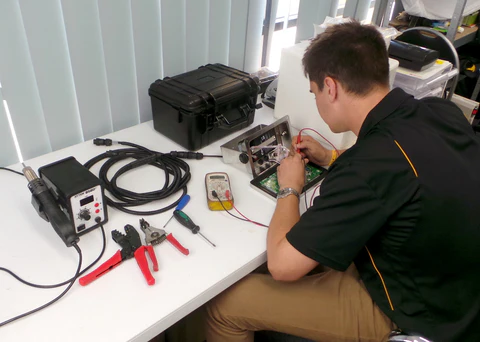
When it comes to industrial operations, precision is everything. Whether you’re working in automotive manufacturing, aerospace engineering, or heavy machinery, accurate torque application ensures the safety, reliability, and efficiency of your equipment. That’s why torque wrench calibration services are crucial to maintaining industrial accuracy.
Why Torque Wrench Calibration Matters
A torque wrench is a precision tool designed to apply a specific force to fasteners. Over time, repeated use can cause these tools to drift out of calibration, leading to inaccurate torque readings. This inaccuracy can result in:
- Loose or overtightened fasteners
- Increased wear and tear on machinery
- Potential safety hazards for workers
- Non-compliance with industry standards
By scheduling regular torque wrench calibration services, you can prevent these issues and maintain operational integrity. If you need to ensure your equipment meets industry regulations, Contact us today for expert calibration services.
How Torque Wrench Calibration Works
The calibration process involves verifying the accuracy of a torque wrench against a certified standard. Professional calibration services typically follow these steps:
Initial Inspection – Checking the wrench for physical damage or worn-out components.
Testing – Using a torque analyzer to measure the current accuracy.
Adjustment & Calibration – Fine-tuning the wrench to ensure it meets the correct specifications.
Certification – Issuing a calibration certificate verifying compliance with industry standards.
For more details on this process, click to read more about how we ensure precision in every calibration.
Benefits of Professional Torque Wrench Calibration
Many businesses assume that as long as a torque wrench functions, it’s accurate. However, professional calibration provides several benefits:
Accuracy – Ensures that your wrench delivers the exact force required.
Compliance – Meets industry regulations such as ISO 6789.
Cost Savings – Prevents costly errors and equipment damage.
Extended Tool Life – Regular calibration keeps tools in optimal condition.
To keep your torque wrenches in peak condition, go to this web-site for professional calibration solutions.
How Often Should You Calibrate Your Torque Wrench?
Calibration frequency depends on several factors, including the wrench’s usage and industry requirements. However, general guidelines recommend:
- Every 5,000 cycles or at least once per year for moderate use.
- Every 2,500 cycles for heavy-duty applications.
- After any mechanical shock (e.g., dropping the wrench).
If you’re unsure about your tool’s calibration needs, Contact us for expert advice.
Choosing the Right Calibration Service
Not all calibration services are equal. When selecting a provider, look for:
- ISO-certified technicians
- Advanced testing equipment
- Fast turnaround times
- Detailed calibration reports
For industry-leading torque wrench calibration services, click to read more about our certified processes and expert solutions.
Final Thoughts
Precision and accuracy in torque application are non-negotiable in industrial settings. By investing in regular torque wrench calibration services, you can enhance safety, improve compliance, and extend the lifespan of your tools. Don’t leave accuracy to chance—go to this web-site to schedule your calibration service today.
For more information, Contact us now and ensure your torque tools meet the highest industry standards!