Mastering the Digital Warehouse: A Comprehensive Guide to Inventory Management Solutions
Transform your business operations with advanced inventory management techniques and cutting-edge warehouse software solutions. Introduction In today’s fast-paced business environment,...
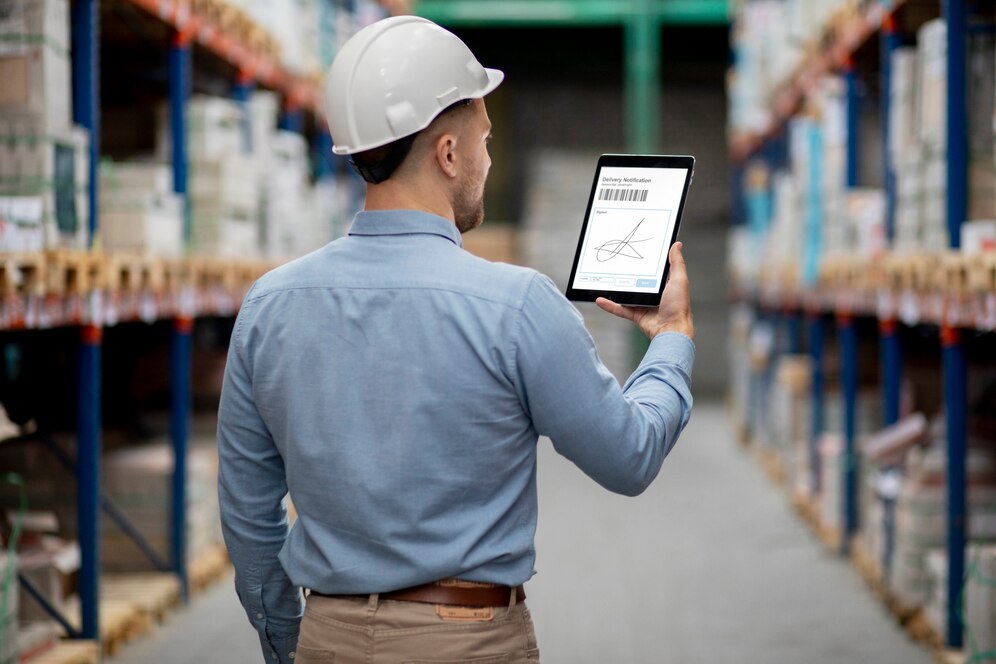
Transform your business operations with advanced inventory management techniques and cutting-edge warehouse software solutions.
Introduction
In today’s fast-paced business environment, effective inventory management has evolved from a simple tracking system to a critical strategic function. Organizations across industries—from retail giants to manufacturing plants and healthcare facilities—have recognized that precise inventory control directly impacts customer satisfaction, operational efficiency, and ultimately, the bottom line. With businesses handling increasingly complex supply chains and facing heightened customer expectations for rapid fulfillment, the margin for error has shrunk dramatically.
The digital transformation of inventory management represents one of the most significant advancements in modern business operations. Gone are the days of paper ledgers and manual counts; today’s inventory management systems leverage sophisticated algorithms, real-time data analytics, and seamless integration capabilities to provide unprecedented visibility and control over stock levels, movements, and forecasting.
This comprehensive guide delves into the world of inventory management and warehouse inventory management software, exploring how these tools have revolutionized the way businesses track, maintain, and optimize their inventory processes. Whether you’re a small business owner looking to implement your first formal inventory system or an enterprise-level operation seeking to enhance your existing infrastructure, this article will provide valuable insights into best practices, emerging technologies, and strategic approaches to inventory management.
We’ll explore the fundamental principles that underpin effective inventory control, examine the transformative impact of purpose-built software solutions, and provide actionable strategies for implementing systems that align with your specific business needs. By the end of this guide, you’ll have a clearer understanding of how modern inventory management practices can drive efficiency, reduce costs, and create sustainable competitive advantages in today’s challenging marketplace.
What Is Inventory Management?
Inventory management encompasses all the processes and systems used to track, control, and maintain an organization’s stock of products. This includes raw materials, components, work-in-progress items, and finished goods that are ready for sale. At its core, inventory management seeks to answer fundamental questions: What do we have? Where is it located? How much do we need? When should we order more?
The Evolution of Inventory Management
The practice of inventory management has undergone significant evolution over the decades:
Traditional Approaches: Historically, businesses relied on periodic physical counts and paper-based systems to track inventory. These methods were labor-intensive, error-prone, and provided only periodic snapshots of inventory status rather than real-time information.
Early Digital Systems: The introduction of computerized inventory management in the 1970s and 1980s represented a significant advancement, allowing businesses to maintain digital records and perform basic analysis of inventory data.
Enterprise Resource Planning (ERP): The 1990s saw the rise of integrated ERP systems that connected inventory management with other business functions such as accounting, purchasing, and sales, providing a more holistic view of operations.
Modern Cloud-Based Solutions: Today’s inventory management systems leverage cloud computing, mobile technologies, and advanced analytics to provide real-time visibility, predictive capabilities, and seamless integration with other business systems.
Core Components of Inventory Management
Effective inventory management encompasses several key components:
Inventory Tracking: The foundation of any inventory management system is accurate tracking of stock levels, locations, and movements. This includes recording all incoming and outgoing inventory transactions, transfers between locations, and adjustments due to damage or obsolescence.
Demand Forecasting: Predicting future demand based on historical data, market trends, seasonal variations, and promotional activities helps businesses maintain optimal inventory levels.
Order Management: This includes determining when to place orders, calculating optimal order quantities, and tracking the status of purchase orders from creation to receipt.
Warehouse Management: Efficient organization of physical storage spaces, including bin locations, picking routes, and storage optimization strategies.
Inventory Optimization: Balancing inventory levels to minimize holding costs while ensuring sufficient stock to meet customer demand and prevent stockouts.
Reporting and Analytics: Generating insights from inventory data to identify trends, potential issues, and opportunities for improvement.
The Strategic Importance of Inventory Management
Far from being merely an operational necessity, inventory management has emerged as a strategic differentiator for businesses. Here’s why it matters:
Financial Impact: Inventory often represents one of the largest assets on a company’s balance sheet. Effective management reduces carrying costs, minimizes write-offs due to obsolescence, and improves cash flow by preventing overstocking.
Customer Satisfaction: Having the right products available when customers want them directly impacts satisfaction and loyalty. In today’s competitive environment, stockouts can quickly lead to lost sales and damaged reputations.
Operational Efficiency: Well-designed inventory management processes reduce the labor required for physical counts, minimize errors in order fulfillment, and streamline receiving and put-away operations.
Supply Chain Resilience: As recent global disruptions have demonstrated, robust inventory management provides businesses with greater flexibility to navigate supply chain challenges and adapt to changing market conditions.
Warehouse Inventory Management Software
Warehouse inventory management software represents the technological backbone of modern inventory control systems. These sophisticated platforms have transformed how businesses track, manage, and optimize their inventory operations, enabling unprecedented levels of accuracy, efficiency, and strategic insight.
Core Functionalities of Warehouse Inventory Management Software
Modern warehouse inventory management solutions offer a comprehensive suite of functionalities designed to address every aspect of inventory control:
Real-Time Inventory Tracking: Unlike traditional systems that might update only periodically, today’s software provides instant visibility into inventory levels across multiple locations. This real-time capability enables more responsive decision-making and reduces the risk of stockouts or overstock situations.
Barcode and RFID Scanning: Advanced scanning technologies allow for rapid, accurate data capture during receiving, picking, packing, and shipping processes. These technologies drastically reduce human error while increasing processing speed.
Lot and Serial Number Tracking: For industries with regulatory requirements or quality control needs, the ability to track products by lot or serial number is crucial. This functionality supports traceability, warranty management, and recall processes if needed.
Automated Reordering: Intelligent systems can automatically generate purchase orders when inventory drops below predetermined thresholds, ensuring continuity of supply without manual intervention.
Multi-Location Management: For businesses operating across multiple warehouses or fulfillment centers, centralized software provides visibility and control across the entire network, allowing for inventory transfers and optimized fulfillment strategies.
Integration Capabilities: Modern warehouse management software typically integrates with other business systems such as e-commerce platforms, point-of-sale systems, accounting software, and shipping carriers, creating a seamless flow of information throughout the organization.
Mobile Accessibility: Cloud-based solutions with mobile interfaces allow warehouse staff to access information and perform transactions from anywhere in the facility using handheld devices, improving efficiency and accuracy.
Advanced Features Driving Innovation
Beyond these core functionalities, leading warehouse inventory management software solutions offer advanced capabilities that further enhance operational excellence:
Predictive Analytics: Using historical data and machine learning algorithms, advanced systems can forecast demand patterns, identify potential supply chain disruptions, and recommend optimal inventory levels.
Slotting Optimization: These tools analyze product characteristics, order patterns, and warehouse layout to determine the most efficient placement of items within the facility, reducing travel time and improving picking efficiency.
Labor Management: Integrated workforce management features help optimize staff scheduling, track productivity, and identify opportunities for process improvement.
3D Warehouse Visualization: Some cutting-edge solutions offer three-dimensional modeling of warehouse spaces, enabling more effective space utilization planning and workflow design.
Simulation Capabilities: Before implementing major changes, businesses can use simulation tools to model different scenarios and predict outcomes, reducing implementation risks.
Benefits of Implementing Warehouse Inventory Management Software
The adoption of specialized inventory management software yields numerous advantages for organizations:
Increased Accuracy: By reducing manual data entry and implementing validation controls, these systems typically achieve inventory accuracy rates of 95% or higher, compared to the 63% average accuracy reported in manual systems.
Cost Reduction: Studies indicate that businesses implementing comprehensive warehouse management software can reduce operating costs by 10-20% through improved labor efficiency, reduced inventory holding costs, and minimized error-related expenses.
Enhanced Customer Service: With better visibility into available inventory and order status, businesses can provide more accurate delivery promises and respond more effectively to customer inquiries.
Scalability: As businesses grow, modern software solutions can scale accordingly, accommodating increased transaction volumes, additional locations, and more complex inventory requirements without major system overhauls.
Data-Driven Decision Making: Comprehensive reporting and analytics tools transform raw inventory data into actionable insights, enabling more informed strategic planning and continuous process improvement.
Key Features to Look for in Inventory Management Systems
When evaluating warehouse inventory management software, businesses should consider several critical features that will determine the system’s effectiveness in meeting their specific needs. The following elements represent the foundation of a robust inventory management solution:
Real-Time Visibility and Tracking
Dashboard Monitoring: Intuitive dashboards that display key metrics and inventory status at a glance help managers maintain awareness of operations without having to run reports.
Search and Filter Capabilities: The ability to quickly locate specific inventory items through advanced search functions streamlines operations and improves response times to customer inquiries.
Movement History: Comprehensive tracking of all inventory movements—including receipts, transfers, and shipments—creates an audit trail that supports accountability and problem resolution.
Order and Procurement Management
Purchase Order Automation: Systems that generate purchase orders based on predefined reorder points or forecast data reduce manual workload and help prevent stockouts.
Supplier Management: Tracking supplier performance metrics such as on-time delivery rates and quality metrics helps businesses make informed sourcing decisions.
Order Status Tracking: Real-time visibility into the status of both purchase orders and customer orders improves communication and planning throughout the supply chain.
Warehouse Operations Optimization
Picking and Packing Guidance: Optimized picking routes and packing instructions increase operational efficiency and accuracy in order fulfillment.
Cross-Docking Capabilities: For businesses looking to minimize handling and storage times, cross-docking functionality coordinates incoming and outgoing shipments for direct transfer.
Returns Processing: Streamlined procedures for handling product returns, including inspection, disposition decisions, and inventory updates, are increasingly important in today’s retail environment.
Reporting and Analytics
Customizable Reports: The ability to create tailored reports addressing specific business questions helps organizations extract maximum value from their inventory data.
Trend Analysis: Historical data visualization tools that identify patterns in sales, inventory levels, and other key metrics support more effective planning.
Exception Reporting: Automated alerts for inventory anomalies—such as sudden demand changes or unexpected stockouts—enable proactive management responses.
Security and Access Control
Role-Based Permissions: Granular control over which users can view or modify different aspects of the system helps maintain data integrity and security.
Activity Logging: Detailed records of user actions within the system support accountability and aid in troubleshooting when issues arise.
Data Encryption: Protection of sensitive inventory and customer information through robust encryption methods safeguards business assets.
Integration Capabilities
API Availability: Well-documented application programming interfaces (APIs) facilitate connections with other business systems such as e-commerce platforms, ERPs, and accounting software.
EDI Support: Electronic Data Interchange capabilities streamline communication with trading partners, reducing manual data entry and associated errors.
Third-Party Marketplace Integration: For businesses selling through multiple channels, seamless connections to platforms like Amazon, eBay, and Walmart Marketplace are essential for maintaining accurate inventory across all sales channels.
Implementing Effective Inventory Management Practices
Beyond selecting the right software solution, successful inventory management requires implementing proven operational practices and strategies. These approaches help organizations maximize the value of their inventory management systems while minimizing costs and risks.
Inventory Classification and Prioritization
ABC Analysis: This classic approach categorizes inventory items based on their value and importance:
- “A” items represent the highest value (typically 20% of items accounting for 80% of value)
- “B” items are of moderate value
- “C” items are low-value but may be numerous
This classification helps businesses allocate appropriate resources and attention to different inventory segments.
FSN Analysis: Categorizing items as Fast-moving, Slow-moving, or Non-moving helps identify which products require different management approaches and stocking levels.
VED Analysis: In industries like healthcare or maintenance, classifying items as Vital, Essential, or Desirable ensures critical supplies receive appropriate priority.
Optimizing Inventory Levels
Economic Order Quantity (EOQ): This mathematical formula calculates the ideal order quantity that minimizes the total of ordering and holding costs, balancing the tradeoffs between order frequency and inventory carrying costs.
Safety Stock Management: Determining appropriate buffer inventory levels based on demand variability, lead time uncertainty, and service level requirements protects against stockouts without excessive inventory investment.
Just-in-Time Approaches: For appropriate product categories, implementing JIT principles reduces carrying costs by synchronizing inventory arrivals with production or sales requirements.
Cycle Counting: Rather than annual physical inventories that disrupt operations, implementing systematic cycle counting programs where subsets of inventory are counted on a rotating schedule improves accuracy while maintaining operational flow.
Warehouse Organization and Layout
Slotting Optimization: Strategic placement of items based on picking frequency, size, weight, and complementary products can significantly reduce travel time and improve picking efficiency.
FIFO/FEFO Implementation: Ensuring First-In-First-Out or First-Expired-First-Out processes are followed prevents obsolescence and quality issues, particularly important for perishable or dated products.
Zone-Based Organization: Dividing warehouse space into functional zones (receiving, storage, picking, packing, shipping) with appropriate equipment and resources for each activity streamlines operations.
Cross-Docking Opportunities: Identifying products that can bypass storage and move directly from receiving to shipping reduces handling costs and accelerates order fulfillment.
Demand Forecasting and Planning
Collaborative Forecasting: Working with customers and suppliers to share demand information improves forecast accuracy and helps all supply chain partners plan more effectively.
Seasonal Adjustment: Incorporating seasonal patterns into forecasting models helps businesses prepare for predictable demand fluctuations without excessive inventory investment.
Promotion Impact Analysis: Understanding how marketing activities affect demand allows for more accurate planning during promotional periods, reducing both stockouts and overstock situations.
Statistical Forecasting Methods: Leveraging techniques such as moving averages, exponential smoothing, and regression analysis improves forecast accuracy compared to simple historical averaging.
Advanced Inventory Management Technologies
The field of inventory management continues to evolve rapidly, with emerging technologies offering new opportunities for efficiency, accuracy, and strategic advantage. Forward-thinking organizations are exploring these innovations to stay ahead of the competition:
Internet of Things (IoT) Applications
Smart Shelves and Bins: Equipped with weight sensors or RFID readers, these solutions automatically detect inventory levels and can trigger replenishment actions without human intervention.
Environmental Monitoring: IoT sensors tracking temperature, humidity, and other conditions help maintain product quality for sensitive items and provide traceability data for compliance purposes.
Connected Equipment: Machinery with built-in diagnostic capabilities can predict maintenance needs and automatically order replacement parts before failures occur, minimizing downtime.
Artificial Intelligence and Machine Learning
Demand Pattern Recognition: AI algorithms can identify complex patterns in historical sales data that might be invisible to human analysts, improving forecast accuracy for products with volatile demand.
Dynamic Reordering: Machine learning models that continuously adjust reorder points and quantities based on evolving demand patterns optimize inventory levels without manual intervention.
Natural Language Processing: AI-powered interfaces allow warehouse staff to interact with inventory systems through voice commands, improving efficiency during picking and counting operations.
Automation and Robotics
Automated Storage and Retrieval Systems (AS/RS): These high-density storage solutions use robots or mechanical systems to retrieve and store items, maximizing space utilization while reducing labor requirements.
Autonomous Mobile Robots (AMRs): Self-navigating robots that can transport inventory throughout warehouses reduce travel time for workers and improve throughput during peak periods.
Collaborative Picking Robots: Working alongside human pickers, these robots can handle routine retrievals while workers focus on more complex tasks, increasing overall productivity.
Blockchain for Supply Chain Transparency
Product Authentication: Blockchain records provide immutable verification of product origins and chain of custody, particularly valuable for high-value items or products subject to counterfeiting.
Shared Inventory Visibility: Permissioned blockchain networks allow supply chain partners to access real-time inventory information across organizational boundaries while maintaining data security.
Smart Contracts: Automated execution of agreements when predefined conditions are met can streamline procurement processes, reducing administrative overhead and delays.
Augmented Reality Applications
Pick-by-Vision: AR glasses that display picking instructions and optimal routes directly in the worker’s field of view increase accuracy and efficiency while reducing training time.
Remote Assistance: AR tools enable remote experts to guide on-site workers through complex procedures or troubleshooting, improving first-time resolution rates.
Space Planning: AR visualizations help warehouse managers optimize layout and slotting decisions by projecting virtual arrangements onto physical spaces before making actual changes.
Industry-Specific Inventory Management Considerations
While core inventory management principles apply broadly, different industries face unique challenges and requirements that influence their approach to inventory control:
Retail and E-commerce
Omnichannel Fulfillment: Retailers must synchronize inventory across physical stores, online platforms, and marketplaces to provide accurate availability information and optimal fulfillment options to customers.
Seasonal Planning: Fashion retailers and others with seasonal merchandise face particular challenges in balancing inventory investment with the risk of obsolescence at season’s end.
Drop-Shipping Integration: Many e-commerce businesses rely on drop-shipping arrangements where suppliers ship directly to customers, requiring special inventory visibility and order routing capabilities.
Manufacturing
Bill of Materials Management: Manufacturers must track complex relationships between raw materials, components, sub-assemblies, and finished goods to ensure appropriate inventory levels throughout the production process.
Work-in-Progress Tracking: Monitoring inventory as it moves through various production stages helps identify bottlenecks and optimize production flow.
MRO Inventory Control: Maintenance, Repair, and Operations supplies require special attention to ensure critical parts are available when needed without excessive investment in rarely-used items.
Healthcare and Pharmaceuticals
Expiration Date Management: Healthcare providers and pharmacies must ensure strict rotation of dated products to prevent administering expired medications or supplies.
Temperature-Controlled Storage: Many medical products require precise environmental conditions, necessitating specialized storage solutions and monitoring systems.
Regulatory Compliance: Healthcare organizations face strict requirements for traceability and documentation of certain inventory items, particularly controlled substances and implantable devices.
Food and Beverage
First-Expired-First-Out (FEFO): Unlike standard FIFO approaches, food distributors must prioritize shipping products with the earliest expiration dates regardless of when they were received.
Batch Traceability: The ability to quickly identify and isolate specific production batches is essential for food safety and recall management.
Cold Chain Management: Maintaining temperature integrity throughout storage and transportation is critical for many food products, requiring specialized inventory tracking with temperature monitoring integration.
Measuring Inventory Management Success
Implementing effective metrics and key performance indicators (KPIs) is essential for evaluating the performance of inventory management systems and identifying opportunities for improvement:
Financial Metrics
Inventory Turnover Ratio: Calculated as cost of goods sold divided by average inventory value, this metric indicates how many times inventory is sold and replaced within a specific period. Higher turnover generally indicates more efficient inventory management.
Days Sales of Inventory (DSI): This measure shows how many days, on average, it takes to sell through inventory. Lower DSI typically indicates better liquidity and reduced carrying costs.
Carrying Cost as Percentage of Inventory Value: Tracking the total costs associated with holding inventory (including storage, insurance, depreciation, and capital costs) relative to inventory value helps quantify the financial impact of inventory decisions.
Operational Metrics
Inventory Accuracy: Measured through cycle counting or physical inventory, this metric compares system inventory records with actual counts. World-class operations typically achieve accuracy rates above 99%.
Perfect Order Rate: This composite metric evaluates the percentage of orders delivered complete, on time, damage-free, and with accurate documentation, providing a holistic view of inventory management effectiveness.
Pick Accuracy: Tracking the frequency of picking errors helps identify training needs or process improvements in warehouse operations.
Stockout Rate: Monitoring the frequency and duration of out-of-stock situations helps balance inventory investment against service level objectives.
Efficiency Metrics
Picking Time per Line: Measuring the average time required to pick each order line helps identify opportunities for layout improvements or process changes.
Put-away Time: Tracking how quickly received items can be properly stored provides insights into receiving process efficiency and warehouse organization.
Space Utilization: Calculating the percentage of available storage space being effectively used helps identify opportunities for better warehouse organization or expansion needs.
Continuous Improvement Approaches
Regular Metric Review: Scheduling routine reviews of key metrics helps maintain focus on inventory performance and identify trends before they become problems.
Benchmarking: Comparing performance against industry standards or best-in-class operators provides context for evaluating current operations and setting improvement targets.
Root Cause Analysis: When metrics indicate problems, systematic investigation of underlying causes rather than symptoms leads to more effective solutions.
PDCA Cycles: Implementing the Plan-Do-Check-Act methodology for improvement initiatives ensures changes are properly evaluated and refined before full implementation.
Case Studies: Successful Inventory Management Transformations
Examining real-world examples of organizations that have successfully transformed their inventory management practices provides valuable insights and inspiration:
Mid-Size Retailer Reduces Carrying Costs by 23%
A regional specialty retailer with 35 locations was struggling with excessive inventory levels and frequent stockouts despite high overall inventory investment. By implementing:
- ABC classification with differentiated service levels
- Automated replenishment based on store-specific demand patterns
- Centralized distribution with cross-docking capabilities
The company reduced overall inventory value by 18% while simultaneously improving in-stock rates from 92% to 98%, resulting in both cost savings and revenue growth.
Manufacturing Company Improves Production Efficiency
A custom equipment manufacturer facing material shortages that caused production delays implemented a comprehensive inventory management solution that included:
- Integration between sales, engineering, and purchasing systems
- Component-level demand forecasting based on sales pipeline
- Vendor-managed inventory arrangements for critical components
The result was a 65% reduction in production delays due to material shortages and a 12% improvement in overall manufacturing throughput.
Healthcare Provider Enhances Patient Safety
A multi-facility healthcare system implemented advanced inventory management for pharmaceuticals and medical supplies, featuring:
- RFID tracking of high-value supplies and equipment
- Integration with electronic medical records for charge capture
- Automated expiration date monitoring and alerts
The organization reduced expired product waste by 78%, improved regulatory compliance, and enhanced patient safety through better tracking of implantable devices and controlled substances.
E-commerce Startup Scales Operations
A rapidly growing direct-to-consumer brand implemented scalable inventory management practices early in its development:
- Cloud-based warehouse management with multi-location capabilities
- Integration with third-party logistics providers for distributed fulfillment
- Real-time inventory synchronization across sales channels
This foundation allowed the company to expand from 200 to 15,000 orders per day within 18 months without significant operational disruptions, maintaining 99.7% order accuracy throughout the growth period.
Future Trends in Inventory Management
As technology evolves and business environments change, several emerging trends are shaping the future of inventory management:
Hyperautomation
The combination of robotics, AI, and process automation technologies is creating increasingly autonomous warehouse operations where routine decisions and activities require minimal human intervention. Industry leaders are implementing:
- End-to-end automation from receiving through shipping
- Self-optimizing systems that continuously refine slotting and picking strategies
- Exception-based management where humans focus only on unusual situations requiring judgment
Micro-Fulfillment Centers
Rather than relying solely on large centralized warehouses, many businesses are establishing smaller fulfillment operations closer to customers:
- Urban micro-warehouses supporting same-day delivery
- Store-based fulfillment centers combining retail and distribution functions
- Automated mini-facilities in strategic locations serving specific market segments
Sustainable Inventory Practices
Environmental considerations are increasingly influencing inventory management decisions:
- Carbon footprint tracking across the supply chain
- Inventory optimization to reduce waste and obsolescence
- Packaging reduction strategies and reusable container systems
- Circular economy approaches that incorporate return flows and remanufacturing
Resilience and Risk Management
Recent global disruptions have highlighted the importance of building resilience into inventory management strategies:
- Strategic safety stocks for critical items
- Diversified sourcing strategies to mitigate supplier risks
- Scenario planning and simulation capabilities for risk evaluation
- Dynamic inventory policies that adapt to changing risk profiles
Predictive and Prescriptive Analytics
Advanced analytics are evolving from descriptive (what happened) to predictive (what will happen) and ultimately prescriptive (what should we do):
- AI-powered demand sensing that incorporates external data sources
- Automated scenario modeling for inventory decision support
- Continuous optimization of inventory parameters without human intervention
Conclusion
Effective inventory management represents a critical competitive advantage in today’s business environment. The integration of advanced warehouse inventory management software with strategic operational practices creates opportunities for significant improvements in efficiency, customer service, and financial performance.
As we’ve explored throughout this comprehensive guide, successful inventory management requires:
- Strategic Alignment: Inventory practices must support broader business objectives related to customer service, financial performance, and operational efficiency.
- Technology Enablement: Modern warehouse inventory management software provides the visibility, automation, and analytical capabilities necessary to optimize complex inventory operations.
- Process Excellence: Even the most sophisticated technology requires well-designed processes and workflows to deliver maximum value.
- Continuous Improvement: The most successful organizations view inventory management as an ongoing journey rather than a one-time implementation project.
- Future Orientation: Staying aware of emerging technologies and trends helps businesses maintain competitive advantage as the inventory management landscape continues to evolve.
By thoughtfully combining these elements into a cohesive approach, organizations can transform their inventory management function from a necessary operational cost center into a strategic asset that drives business success. Whether you’re just beginning your inventory management journey or looking to enhance an established system, the principles and practices outlined in this guide provide a foundation for achieving world-class performance in this critical business function.
FAQs
What is inventory management and why is it important?
Inventory management encompasses all the processes and systems used to track, control, and optimize an organization’s stock of products, materials, and components. It’s important because effective inventory management directly impacts financial performance through reduced carrying costs and improved cash flow, enhances customer satisfaction by ensuring product availability, and increases operational efficiency by streamlining warehouse operations and reducing labor costs.
How does warehouse inventory management software differ from basic inventory tracking?
Warehouse inventory management software goes far beyond basic inventory tracking by offering comprehensive functionality including real-time visibility across multiple locations, advanced forecasting capabilities, automated replenishment, integration with other business systems, optimization of warehouse operations, detailed analytics and reporting, and support for complex inventory strategies such as cross-docking and zone-based management.
What are the most common inventory management challenges businesses face?
Common inventory management challenges include balancing inventory levels to avoid both stockouts and excess inventory, maintaining accurate inventory records, forecasting demand effectively, managing seasonal fluctuations, handling product returns efficiently, coordinating inventory across multiple locations, adapting to changing customer expectations for rapid fulfillment, and managing inventory across multiple sales channels.
How can small businesses implement effective inventory management without significant investment?
Small businesses can implement effective inventory management by starting with cloud-based software solutions that offer flexible pricing models, prioritizing core functionalities rather than advanced features, implementing basic best practices like ABC classification and cycle counting, focusing on high-value inventory items first, leveraging mobile technology for improved accuracy, and gradually expanding capabilities as the business grows and ROI is demonstrated.
What metrics should businesses track to evaluate inventory management performance?
Key metrics for evaluating inventory management performance include inventory turnover ratio, days sales of inventory, carrying cost as a percentage of inventory value, inventory accuracy, perfect order rate, stockout frequency, fill rate, pick accuracy, order cycle time, and return rate. The specific metrics most relevant to a particular business will depend on its industry, size, and strategic priorities.