How Length Stop Measuring Systems Support Quality Control in Packaging
Customer satisfaction and operational effectiveness in the fast-paced packaging sector of today depend on quality control being assured. Length Stop...
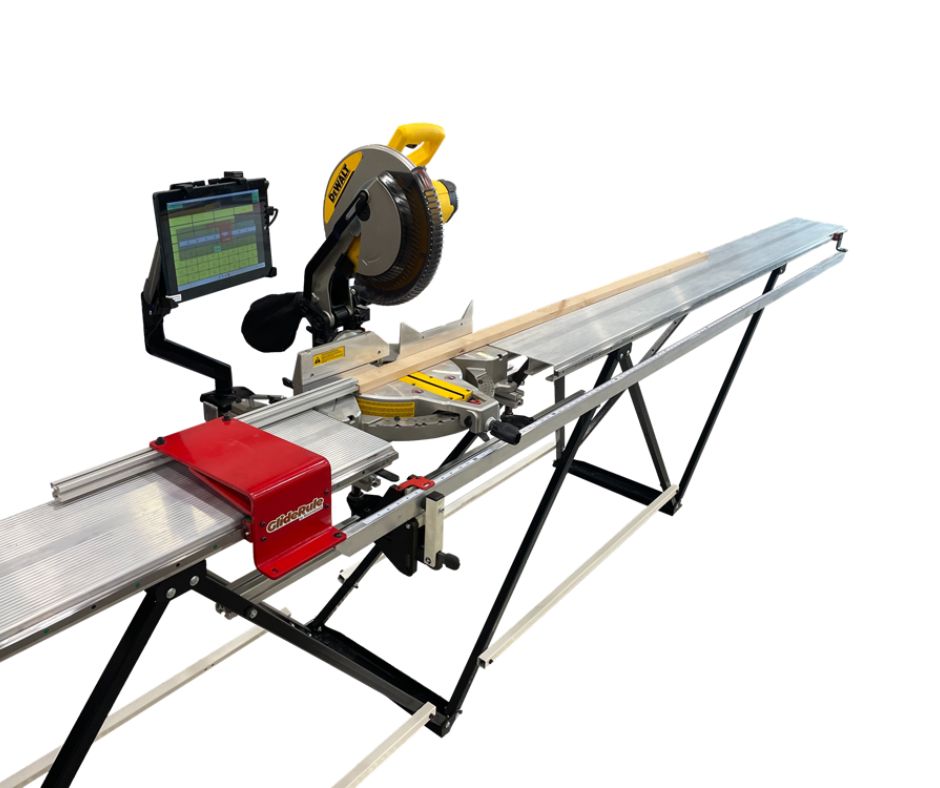
Customer satisfaction and operational effectiveness in the fast-paced packaging sector of today depend on quality control being assured. Length Stop Measuring Systems are one technical development greatly impacting this field. These devices are meant to improve measuring consistency and accuracy over several cutting and packaging uses. Precise measuring equipment become far more important in both manual and automated procedures as packaging companies progressively automate their operations. Length Stop Measuring Systems are increasingly essential instruments in preserving high-quality standards—from lowering material waste to enhancing the consistency of packed goods.
Improving Measurement Reliability and Accuracy
Length Stop Measuring Systems’ Part in Quality Control
Maintaining consistency in packaging dimensions depends on dependable measurement accuracy offered by length stop measuring systems. Perfect lengths are required whether cutting metal packing components, plastic wraps, or corrugated cardboard to prevent fitting problems, waste, or misaligned goods. In sectors where accurate matching of packaging proportions to certain product specifications is required, even a small departure might result in expensive mistakes. Combining these solutions will help businesses create a repeatable procedure that guarantees every cut is exactly the same independent of operator expertise or tiredness.
Mining Human Mistakes and Increasing Repeatability
Among the main causes of quality control issues is human mistake. By automating the measuring process, Length Stop Measuring Systems eliminate the typically erratic nature of hand measurements. The technology will direct the cutting tool to the precise measurement every time operators just provide the intended length. This not only lowers rework and scrap but also makes consistent package quality possible—critical for both regulatory compliance and consumer expectations.
Simplifying Procedures and Minimising Outbreaks
Faster Setup and Enhanced Effectiveness
Length Stop Measuring Systems have one of the benefits in their capacity to simplify processes. Conventional measuring and marking techniques can be error-prone and time-consuming, therefore slowing down output. Workers may move between jobs more quickly and begin cutting right away with little setup if a measurement system is in place. Shorter lead times and faster order fulfilment resulting from this degree of efficiency are both vital for packaging industry competitiveness.
Integration for Smart Operations Using Cutting List Software
Integrating Length Stop Measuring Systems with cutting list software offers still another significant advantage. This combo lets cut lengths, amounts, and material optimisation be totally digital under control. Cutting list software guarantees the most effective use of resources by compiling an optimal list for the measuring system to follow from product specifications. By computing the ideal cutting patterns, it minimises waste and lowers the possibility of human error during hand measurement entry.
The combination of the measuring device and the software lets operators operate big batches without physically changing the system between cuts. This degree of automation is particularly appreciated by packaging firms managing several product SKUs and sizes. It guarantees exact and consistent matching of every item cut to the intended dimensions.
Maximising Resources and Minimising Waste
Savings by Using Correct Materials
A major cost consideration in packaging operations is material waste. Cutting mistakes can lead to wasted goods that have to be thrown away or recycled—an ineffective and expensive result. Using Length Stop Measuring Systems helps businesses exactly regulate material usage, therefore minimising offcuts and maximising yield. Particularly in high-volume manufacturing settings, these savings over time can significantly affect a company’s bottom line.
Waste Reduction’s Environmental Effects
Reducing material waste advances environmental objectives in addition to saving money. Many of the packaging companies are striving for greener operations by reducing their environmental impact. Length Stop Measuring Systems are quite important in supporting environmentally friendly procedures by increasing material accuracy and lowering thrown-off quantities. Furthermore, by allowing better use of resources, these solutions help businesses match consumer expectations for ethical production and environmental compliance criteria.
Enhancing Traceability and Compliance
Confidently Meeting Industry Standards
Packaging quality management is about industry standards as much as consumer delight. By helping items to be packaged within defined tolerances, length stop measuring systems help to lower the risk of non-industry standard non-compliance. For many items, particularly in sectors including food, medicines, and electronics where container size, seal integrity, and consistency must follow rigors standards, accurate packaging measurements are absolutely vital.
Quality Audits: Data Logging
Data logging features abound in many contemporary length stop measuring systems. These tools let businesses log measurement data for every cut they do. For certification processes and quality audits, where thorough documentation is needed to show compliance with quality control methods, this degree of traceability is especially helpful. Maintaining a digital trail helps businesses to rapidly spot where problems might have started and act appropriately.
Enhancing Training and Workforce Productivity
Simplifying Operator Education
Advanced measuring systems help operators to rely less on specific training. The Length Stop Measuring System manages the precision, so enabling new hires to be onboarded faster and existing staff members to perform more effectively. Simplified controls and digital displays let employees focus more on throughput and quality assurance and spend less time measuring and adjusting.
Reducing Rework and Boosting Productivity
These solutions reduce rework needed because of improper package sizes by removing measurement and cutting mistakes. This guarantees effective utilisation of labour hours and maximum capacity of equipment. Maximising staff efficiency via clever technologies like Length Stop Measuring Systems becomes a major competitive advantage in a labor-constrained environment.
Ultimately, Precision for Long-Term Quality Requires Investments
Length Stop Measuring Systems are proving to be a wise investment for packaging firms in a sector where accuracy, efficiency, and consistency rule most. By guaranteeing accurate measurements, lowering waste, and smooth integration with tools like cutting list software to automate and maximise the whole cutting process, these solutions greatly help to regulate quality. Through better material use, streamlining processes, and support of compliance, they enable businesses to remain competitive in a changing environment.
Adopting automation and precision tools is no more a luxury as demand for tailored, premium packaging keeps rising; it is rather a need. With consistent results, lower costs, and a more sustainable production process, length stop measuring systems help producers to confidently meet that demand. Using these technologies can help you improve your quality standards regardless of size—small packing shop or large-scale facility—while also increasing output and profitability.