How Do Environmental Factors Affect the Need for Downhole Tool Repair
Downhole tools play an essential role in the oil and gas industry. These tools are used in drilling and extraction...
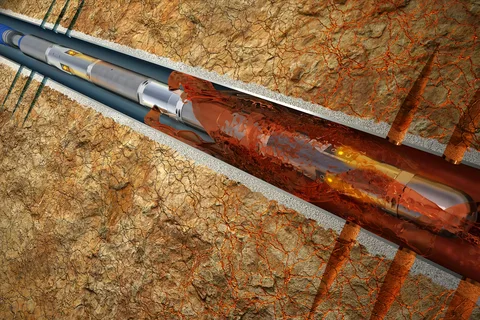
Downhole tools play an essential role in the oil and gas industry. These tools are used in drilling and extraction processes, working deep beneath the Earth’s surface. Over time, the harsh environments in which these tools operate can lead to wear and tear, causing them to need repair. Understanding how environmental factors influence the need for downhole tool repair is crucial to maintaining equipment and ensuring smooth operations. In this blog, we will explore these factors in simple language and with clear explanations.
What Are Downhole Tools?
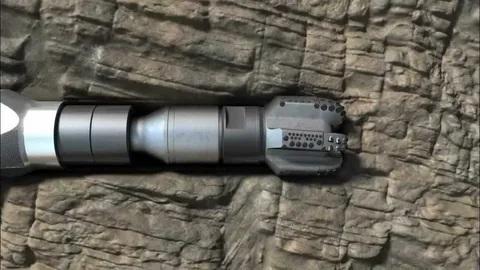
Downhole tools are specialized equipment used in drilling, production, and intervention operations in oil and gas wells. These tools are lowered into the wellbore to perform specific functions, such as drilling, measuring, or extracting resources. The tools must withstand extreme conditions deep underground, including high pressure, high temperatures, and exposure to corrosive materials. While these tools are built to be durable, environmental factors can still impact their performance and lifespan.
Types of Downhole Tools
There are several types of downhole tools used in different phases of drilling and extraction:
- Drilling Tools: These tools help in drilling the wellbore. Examples include drill bits, stabilizers, and reamers.
- Measurement Tools: These tools measure conditions such as pressure, temperature, and flow rates within the well. Examples include pressure gauges and temperature sensors.
- Completion Tools: These tools are used to complete the well and prepare it for production. Examples include packers and valves.
- Intervention Tools: These tools are used to maintain or repair the well after it has been completed. Examples include fishing tools and wireline tools.
Now that we understand the types of downhole tools, let’s explore how environmental factors affect their need for repair.
Major Environmental Factors Affecting Downhole Tools
Downhole tools operate in challenging environments, and several environmental factors can lead to the need for repair. These factors include:
- Temperature
- Pressure
- Corrosion
- Erosion
- Vibration and Shock
- Chemical Exposure
Each of these factors affects the performance and durability of downhole tools. Let’s discuss them one by one.
1. Temperature
How High Temperatures Impact Downhole Tools
The temperatures in oil and gas wells can reach extremely high levels, sometimes exceeding 300°C (572°F). High temperatures can cause several problems for downhole tools:
- Material Degradation: Metals and other materials used in downhole tools can weaken or deform when exposed to high temperatures over time. This can reduce the tool’s strength and increase the likelihood of failure.
- Thermal Expansion: Materials expand when heated, and this can cause components of the tool to become misaligned or damaged.
- Seal Failure: Many downhole tools rely on seals to keep fluids and gases in place. High temperatures can cause seals to wear out or fail, leading to leaks.
How to Address Temperature-Related Damage
To minimize the impact of high temperatures, downhole tools are often made from heat-resistant materials such as stainless steel, titanium, or specialized alloys. Regular inspections are also necessary to identify signs of temperature-related damage early and prevent major failures.
2. Pressure
How High Pressure Affects Downhole Tools
Oil and gas wells are located deep underground, where the pressure is incredibly high. Downhole tools must be able to withstand these pressures, which can reach several thousand pounds per square inch (psi). High pressure can cause the following issues:
- Structural Damage: If a tool is not designed to handle the high pressure, it may crack, collapse, or burst.
- Seal Compromise: Like with high temperatures, seals can fail under extreme pressure, leading to tool malfunction.
How to Address Pressure-Related Damage
To prevent pressure-related damage, downhole tools are designed with high-strength materials and are thoroughly tested to ensure they can withstand the specific pressures they will encounter. Regular maintenance is crucial to ensure that tools remain structurally sound.
3. Corrosion
How Corrosion Damages Downhole Tools
Corrosion occurs when metals react with chemicals in the environment, such as water, hydrogen sulfide, or carbon dioxide. In downhole environments, tools are often exposed to corrosive materials, which can gradually wear away the metal surfaces, leading to:
- Material Weakening: As the metal corrodes, it becomes thinner and weaker, making the tool more likely to fail.
- Pitting: Corrosion can cause small holes or pits to form on the tool’s surface, leading to further deterioration.
How to Address Corrosion-Related Damage
To combat corrosion, downhole tools are often coated with protective materials or made from corrosion-resistant alloys. Regular inspections and maintenance help detect early signs of corrosion so that repairs can be made before the tool fails completely.
4. Erosion
How Erosion Affects Downhole Tools
Erosion occurs when fluids or solid particles, such as sand or rock, move rapidly past the surface of a downhole tool, wearing it away over time. Erosion is particularly common in wells with high fluid flow rates or where abrasive materials are present. This can lead to:
- Material Loss: Over time, the tool’s material can be worn away, weakening its structure.
- Surface Roughness: Erosion can create a rough surface, which may lead to inefficient tool performance or cause additional wear on other parts of the tool.
How to Address Erosion-Related Damage
To minimize the effects of erosion, downhole tools may be designed with harder materials or coatings that resist wear. It is also important to monitor the flow rates and composition of the well’s fluids to reduce erosion risk.
5. Vibration and Shock
How Vibration and Shock Impact Downhole Tools
Downhole tools are often subjected to intense vibration and shock during drilling and production operations. The movement of the drill string or other equipment can cause vibration, while sudden impacts can create shock forces. These forces can lead to:
- Fatigue Failure: Repeated vibration can cause materials to fatigue and eventually break.
- Component Misalignment: Shock forces can cause components to shift or become misaligned, leading to tool failure.
How to Address Vibration and Shock-Related Damage
To reduce the risk of vibration and shock damage, downhole tools are often designed with dampening features that absorb or reduce the forces. Additionally, regular maintenance and monitoring help identify early signs of fatigue or misalignment.
6. Chemical Exposure
How Chemicals Affect Downhole Tools
In oil and gas wells, downhole tools are often exposed to various chemicals, such as acids, alkalis, and hydrocarbons. These chemicals can react with the materials of the tool, leading to:
- Chemical Degradation: Certain chemicals can cause the materials to break down, weakening the tool’s structure.
- Seal Damage: Chemical exposure can also cause seals and other non-metallic components to deteriorate.
How to Address Chemical-Related Damage
To protect against chemical exposure, downhole tools are often made with materials that are resistant to the specific chemicals present in the well. Regular inspections and maintenance can help detect early signs of chemical damage, allowing for timely repairs.
How Regular Maintenance Reduces the Need for Major Repairs
While environmental factors can cause significant damage to downhole tools, regular maintenance is key to minimizing the need for major repairs. By performing routine inspections and addressing small issues before they become major problems, companies can extend the lifespan of their tools and avoid costly downtime.
Importance of Inspection and Monitoring
Regular inspections allow companies to detect early signs of damage, such as corrosion, erosion, or fatigue. By monitoring the performance of downhole tools and keeping track of environmental conditions, companies can predict when a tool is likely to need repair or replacement.
Repair vs. Replacement
In some cases, downhole tools can be repaired to restore their functionality. In other cases, the damage may be too severe, and the tool will need to be replaced. Making the right decision between repair and replacement depends on the extent of the damage and the cost-effectiveness of the repair.
Conclusion
Environmental factors such as temperature, pressure, corrosion, erosion, vibration, shock, and chemical exposure play a significant role in the need for downhole tool repair. Understanding how these factors affect tool performance can help companies take proactive measures to prevent damage, reduce repair costs, and extend the lifespan of their tools. Regular maintenance, inspections, and the use of high-quality materials are crucial to ensuring that downhole tools continue to operate effectively in harsh environments.
For more insightful articles related to this topic, feel free to visit thenewsus.com