Why Malaysian Manufacturers Should Integrate HAZOP into Preventive Maintenance
Discover why integrating HAZOP into preventive maintenance programs is essential for Malaysian manufacturers aiming to improve safety, reduce risks, and...
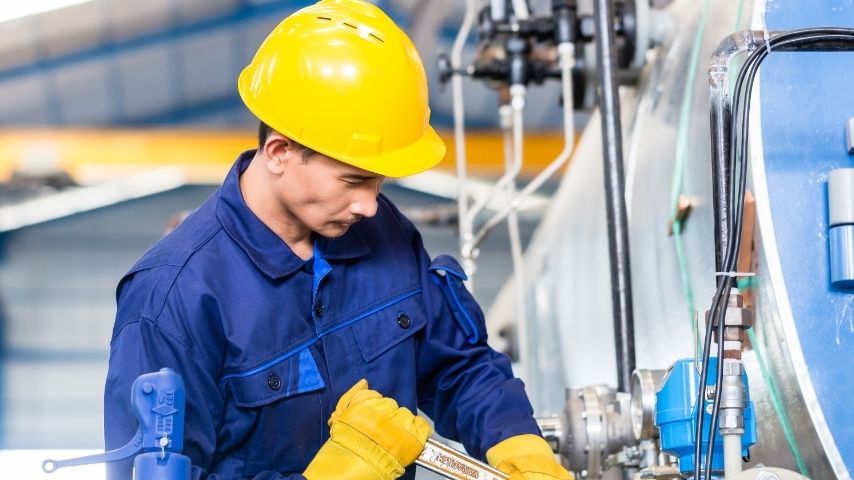
HAZOP integration is crucial for Malaysian manufacturers to enhance their preventive maintenance programs and minimize operational risks.
Are you a Malaysian manufacturer struggling to maintain optimal safety standards while ensuring operational efficiency? The integration of Hazard and Operability Study (HAZOP) into your preventive maintenance strategy could be the game-changer you need.
Let’s explore how HAZOP integration can transform your preventive maintenance strategy, reduce operational risks, and create a safer manufacturing environment. Whether you’re new to HAZOP or looking to improve your existing processes, this guide will provide valuable insights for implementation.
Understanding HAZOP and Its Role in Manufacturing
A HAZOP (Hazard and Operability) study is a systematic examination of industrial processes to identify potential hazards and operational problems. This structured methodology helps manufacturing facilities prevent accidents, improve safety, and optimize operational efficiency.
Core Components of HAZOP Analysis
The foundation of an effective HAZOP study lies in its systematic approach to analyzing process deviations. This methodology breaks down complex industrial processes into manageable sections called nodes, which are then examined using specific guidewords.
A comprehensive operability study involves several key elements working together:
- Study Node Selection: Breaking down the process into logical sections
- Guide Words: Using standardized terms like “more,” “less,” or “none”
- Process Parameters: Analyzing variables such as flow, temperature, and pressure
- Deviation Identification: Examining potential departures from design intent
- Consequence Assessment: Evaluating the impact of identified deviations
The HAZOP team plays a crucial role in this analysis. Typically comprising process engineers, operators, safety specialists, and maintenance personnel, they bring diverse perspectives to identify potential hazards and operational issues.
During the analysis, each node undergoes detailed examination using guide words to identify possible deviations. The team then evaluates:
- Potential causes of deviations
- Consequences if deviations occur
- Existing safeguards
- Recommended actions for improvement
This systematic approach ensures thorough coverage of potential hazards while maintaining focus on operational efficiency. The findings from a HAZOP study directly inform maintenance strategies and safety protocols, making it an invaluable tool for manufacturing facilities.
What is HAZOP and why does it matter for workplace safety? Learn more in this comprehensive article.
The Current State of Malaysian Manufacturing Safety
The manufacturing sector in Malaysia has experienced significant growth, yet safety remains a critical concern. Recent studies indicate that Malaysian industries face ongoing challenges in maintaining robust safety protocols despite stringent regulations.
Common Safety Challenges in Malaysian Manufacturing
Malaysian companies often struggle with implementing comprehensive safety measures due to various factors. One primary challenge is the inconsistent adherence to safety standards across different facilities. While larger manufacturers typically maintain strict protocols, smaller operations sometimes fall short of meeting required benchmarks.
The Malaysian industry has seen a concerning trend in workplace incidents, particularly in sectors involving heavy machinery and chemical processing. Statistics from the Department of Occupational Safety and Health (DOSH) highlight that manufacturing accounts for a significant percentage of workplace accidents.
Many facilities face difficulties in:
- Maintaining up-to-date safety documentation
- Providing regular safety training to workers
- Implementing preventive maintenance schedules
- Meeting international safety standard requirements
Despite these challenges, there’s a growing awareness among Malaysian companies about the importance of workplace safety. Industry leaders are increasingly investing in advanced safety systems and training programs to protect their workforce and assets.
The regulatory landscape continues to evolve, with authorities implementing stricter guidelines to ensure compliance. However, the gap between regulation and implementation remains a significant concern for many manufacturers.
Benefits of Integrating HAZOP with Preventive Maintenance
Enhanced Risk Management
Integrating HAZOP with preventive maintenance creates a robust framework for comprehensive risk management in manufacturing facilities. This integration allows organizations to identify potential hazards systematically while maintaining equipment reliability and operational efficiency.
By combining these approaches, manufacturers can proactively address both process-related risks and equipment-specific vulnerabilities. The systematic analysis of potential deviations through HAZOP complements routine maintenance checks, creating a more thorough safety improvement strategy.
The integration enables maintenance teams to prioritize critical equipment based on risk assessment findings. This targeted approach ensures that high-risk areas receive enhanced attention during maintenance schedules, reducing the likelihood of unexpected failures and safety incidents.
Improved Operational Performance
When HAZOP methodology is incorporated into preventive maintenance programs, it significantly enhances operational performance through multiple channels. The systematic evaluation of process parameters helps identify efficiency bottlenecks that might be overlooked in standard maintenance routines.
This integrated approach promotes continuous improvement by establishing clear connections between process deviations and maintenance requirements. Maintenance teams can better understand how equipment conditions affect process safety, leading to more effective maintenance planning and execution.
The combination also optimizes resource allocation by identifying areas where maintenance efforts will have the maximum impact on both safety and performance. This strategic alignment helps organizations achieve better returns on their maintenance investments while maintaining high safety standards.
Regular HAZOP reviews within the maintenance framework provide valuable insights into equipment behavior and potential failure modes. This information helps in refining maintenance schedules and procedures, ultimately leading to improved equipment reliability and reduced downtime.
The integration also facilitates better communication between operations and maintenance teams, as both groups work together to identify and address potential hazards. This collaborative approach enhances overall plant safety while maintaining optimal performance levels.
Implementation Strategy for HAZOP Integration
Team Formation and Training
Implementing HAZOP integration into preventive maintenance requires a systematic and proactive approach, starting with assembling the right team and providing comprehensive training. The success of HAZOP implementation heavily depends on having a well-structured team with diverse expertise.
A cross-functional team should include maintenance engineers, process operators, safety specialists, and quality control personnel. Each member brings unique insights and perspectives, contributing to a more thorough hazard identification process. As a best practice, team members should have at least 5 years of relevant industry experience.
Training is crucial for effective HAZOP integration. Team members need thorough understanding of:
- HAZOP methodology and guidewords
- Process parameters and deviations
- Risk assessment techniques
- Documentation procedures
- Communication protocols
Regular training sessions should focus on systematic risk identification methods and practical application scenarios. This ensures team members can effectively identify potential hazards and propose appropriate preventive measures.
To maintain consistency and efficiency, establish clear roles and responsibilities within the team:
- HAZOP Leader: Guides the study and ensures methodology adherence
- Scribe: Documents findings and recommendations
- Technical Experts: Provide process-specific insights
- Operations Representative: Shares practical operational experience
Continuous improvement is essential. Schedule periodic refresher training sessions to keep the team updated on industry best practices and emerging methodologies. This proactive approach helps maintain high standards of hazard identification and risk assessment.
Also read: Industry-Recognized Elevated Work Platforms Training – Safety and Certification for Work at Heights
Regulatory Compliance and Standards
Malaysian Manufacturing Regulations
In Malaysia’s manufacturing sector, regulatory compliance plays a vital role in ensuring operational safety and environmental protection. The Department of Occupational Safety and Health (DOSH) enforces strict guidelines that manufacturers must follow, particularly concerning hazard identification and risk assessment processes.
The Occupational Safety and Health Act 1994 (OSHA) mandates regular safety assessments, including HAZOP studies, for high-risk manufacturing facilities. This environmental law framework requires manufacturers to maintain detailed documentation of their safety procedures and risk mitigation strategies.
Manufacturers must also align with international standard requirements, such as ISO 45001 for occupational health and safety management systems. These standards provide a structured approach to identifying and controlling workplace hazards, making HAZOP implementation more systematic and effective.
The Environmental Quality Act 1974 (EQA) further reinforces the need for comprehensive hazard analysis in manufacturing processes. Companies must demonstrate their commitment to environmental protection through regular assessments and updates to their safety protocols.
Recent amendments to Malaysian regulations have emphasized the importance of preventive maintenance programs integrated with hazard analysis. This approach helps manufacturers maintain compliance while proactively identifying potential risks before they become serious issues.
Maintaining Effective HAZOP Systems
Documentation and Review Processes
Maintaining robust documentation and conducting regular HAZOP reviews are crucial elements in sustaining an effective hazard prevention system. A well-structured documentation process serves as the foundation for tracking and analyzing potential risks in manufacturing operations.
Regular HAZOP review sessions should be scheduled at predetermined intervals, typically every 3-5 years or when significant process changes occur. These reviews help ensure that all safety measures remain current and effective. During these sessions, teams should meticulously examine existing documentation, including process flow diagrams, piping and instrumentation diagrams, and operating procedures.
The documentation process should include:
- Detailed records of all identified hazards
- Implementation status of recommended actions
- Changes in operating procedures
- Training records of personnel involved
- Incident reports and investigation findings
Ongoing support from management is essential to maintain the effectiveness of HAZOP systems. This includes providing necessary resources, ensuring team availability for regular reviews, and implementing recommended safety measures promptly.
To enhance the review process, manufacturers should:
- Establish clear review schedules
- Maintain updated process documentation
- Track implementation of safety recommendations
- Document all modifications and their impact
- Ensure proper communication of changes to relevant personnel
Building a Safety-First Culture
Employee Engagement and Training
Creating a culture of safety begins with comprehensive employee engagement and effective training programs. In the field of process safety, every team member must understand their role in maintaining a safe working environment. This starts with regular training sessions that go beyond basic safety protocols.
Maintenance personnel need to be actively involved in safety discussions and decision-making processes. This involvement helps create a sense of ownership and responsibility towards safety practices. Regular toolbox talks, safety meetings, and hands-on workshops can significantly improve engagement levels.
To build a robust safety culture, organizations should:
- Implement regular safety awareness programs
- Conduct periodic skill assessments
- Provide hands-on training with safety equipment
- Encourage reporting of near-misses and potential hazards
- Recognize and reward safety-conscious behavior
It’s crucial to ensure that safety training isn’t just a one-time event but an ongoing process. Regular refresher courses help maintain awareness and keep safety protocols fresh in everyone’s minds. This continuous learning approach helps embed safety practices into daily operations.
Creating feedback channels where employees can voice their safety concerns without fear of repercussion is essential. This open communication fosters trust and demonstrates the organization’s commitment to workplace safety.
Organizations should also consider:
- Developing mentorship programs for new employees
- Creating safety committees with rotating membership
- Implementing regular safety audits with employee participation
- Establishing clear communication channels for safety concerns
- Providing resources for continuous safety education
Conclusion
The integration of HAZOP into preventive maintenance represents a crucial step forward for Malaysian manufacturers committed to operational excellence and safety. By adopting this systematic approach, companies can significantly enhance their risk management capabilities while ensuring compliance with regulatory requirements. Through regular HAZOP reviews and a proactive approach to safety, manufacturers can create a robust culture of safety that protects both personnel and assets. The implementation of structured hazard identification processes, coupled with comprehensive risk assessments, enables organizations to stay ahead of potential process deviations and maintain optimal operational efficiency. Take the first step towards transforming your maintenance strategy by incorporating HAZOP methodologies. Start by assembling a multidisciplinary team, establishing regular review schedules, and implementing systematic risk identification procedures. Remember, the journey to enhanced industrial safety is continuous, and HAZOP integration serves as a cornerstone for sustainable manufacturing excellence in Malaysia’s evolving industrial landscape.