From Dust to Detail: Why Post-Construction Cleaning Requires More Than a Mop
Post-construction cleaning isn’t just about wiping down surfaces and disposing of the trash. It’s about preparing a facility for immediate, safe,...
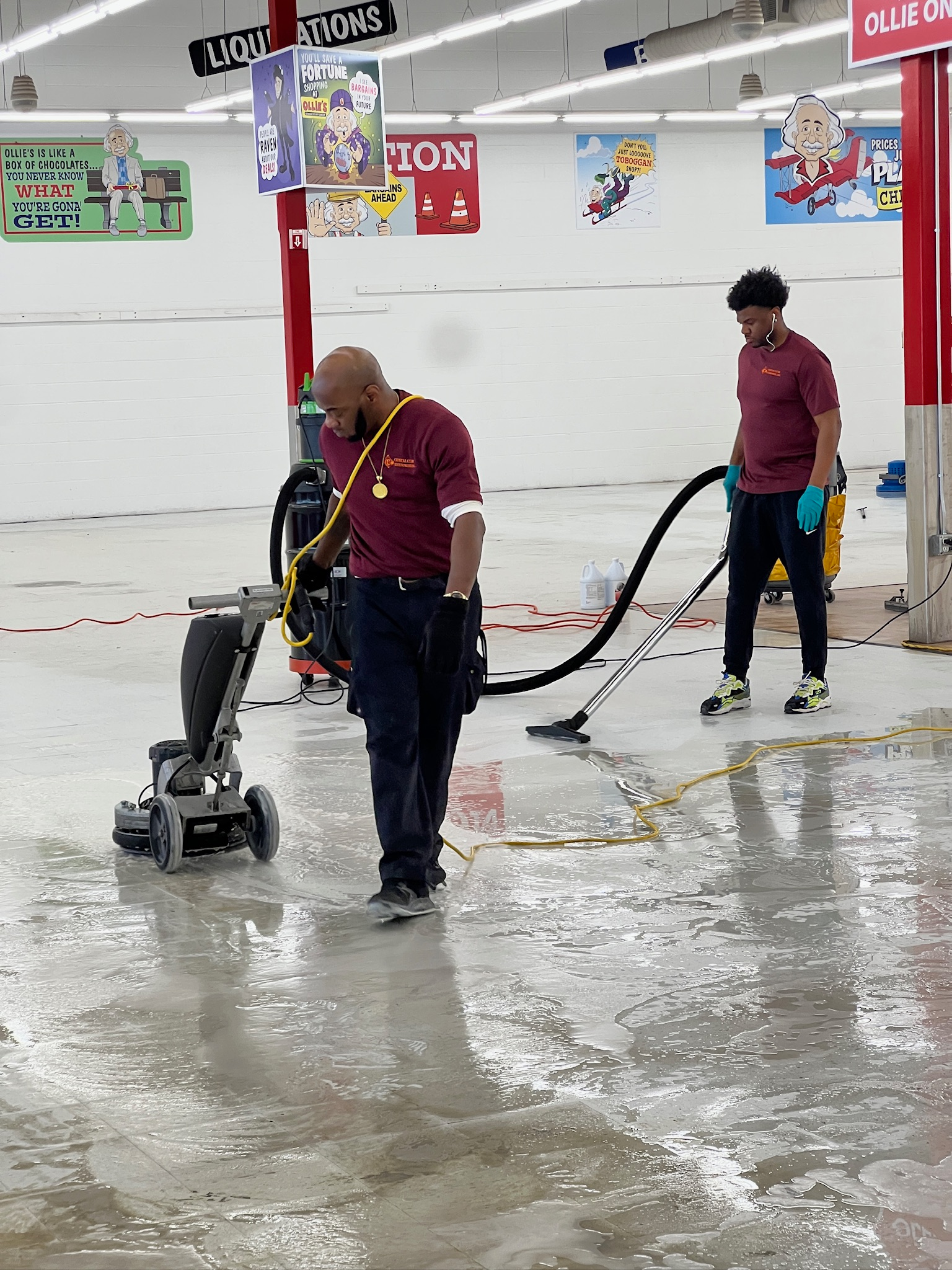
Post-construction cleaning isn’t just about wiping down surfaces and disposing of the trash. It’s about preparing a facility for immediate, safe, and efficient use. While basic janitorial services may seem quick, they fall short in dealing with fine particulate dust, adhesive residues, and construction-specific debris that can linger long after the last contractor leaves. This is where specialty post-construction cleaning becomes necessary, especially for facility managers overseeing operations in manufacturing, distribution, or medical sectors.
Fine Dust: The Hidden Hazard
Construction projects generate an overwhelming amount of fine dust. Drywall installation, sanding, and even general traffic from contractors can produce particles that settle deep into air ducts, surfaces, and carpets. Unlike visible debris, this fine dust isn’t easily handled by basic cleaning tools. Facility managers often assume a mop or vacuum is enough, but these methods rarely address the root of the issue.
Fine dust can affect HVAC systems, reduce indoor air quality, and pose respiratory hazards to employees. This is particularly concerning in manufacturing or distribution centers, where air quality can directly impact worker productivity and equipment function. Specialty cleaning services are equipped with commercial-grade HEPA vacuums and negative air machines that remove these fine particles at the source. Proper removal isn’t just about aesthetics—it’s a safety requirement.
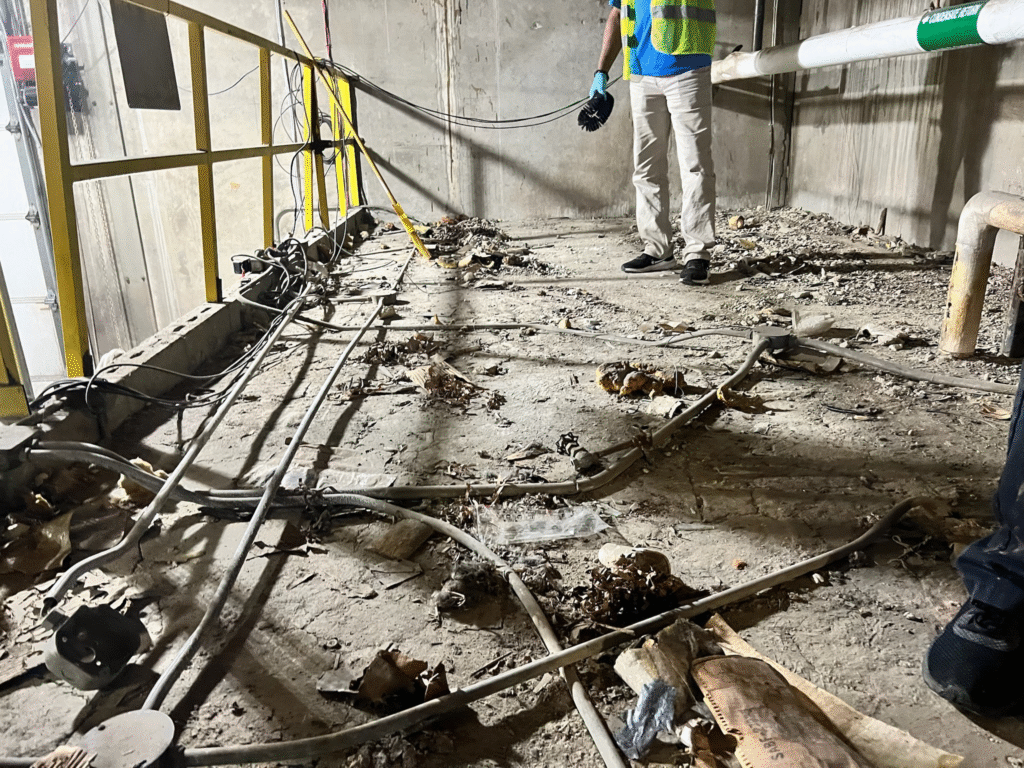
Residue Removal Needs More Than Surface Cleaning
Adhesive residue from tape, stickers on new fixtures, paint overspray, and silicone used during sealing processes all require targeted cleaning. Generic janitorial crews often lack the supplies or knowledge to remove these materials without damaging surfaces. Specialty post-construction cleaners use solvent-safe methods designed for specific materials such as glass, tile, concrete, and stainless steel.
This level of cleaning is especially important in facilities where safety compliance and material integrity are non-negotiable. For example, in a distribution center, improperly cleaned floors may become slip hazards. In medical-related facilities, residue left on newly installed fixtures could interfere with sanitation protocols. Having a crew trained in specialty cleaning processes makes a difference between a space that’s visually complete and one that is fully operational.
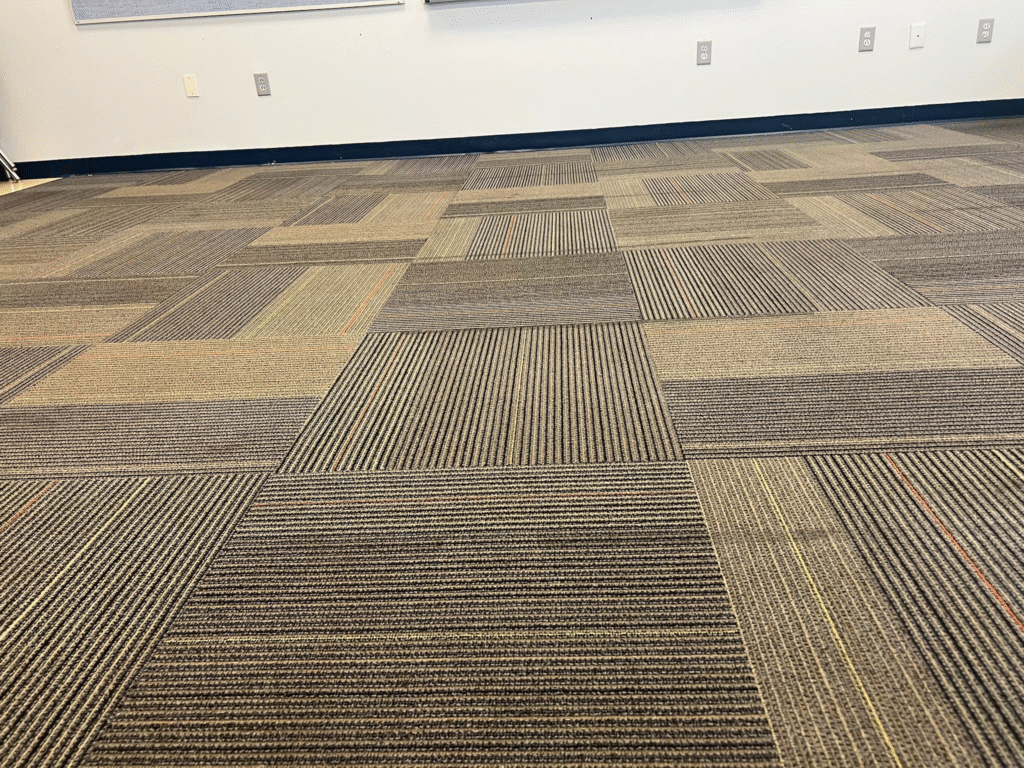
Floor and Carpet Readiness: A Separate Operation
One of the most overlooked areas after construction is floor care. Whether it’s concrete, tile, vinyl, or carpet, each surface needs to be prepared for long-term use. Debris from construction can grind into floor coatings and carpet fibers, shortening the lifespan of expensive installations. Specialty cleaners understand how to prep each flooring type for final use, including buffing, sealing, or deep cleaning carpets.
For example, Office Carpet Cleaning Kansas City facilities need post-project carpet extraction to remove embedded dust and construction residue. Regular janitorial services may only conduct surface-level vacuuming, which won’t preserve flooring investments. Floor cleaning services Kansas City providers trained in post-construction protocols bring the necessary machines and techniques to handle the job correctly from the start.
Compliance and Final Inspection Standards
In medical manufacturing and distribution industries, post-construction cleaning is often part of the final compliance checklist. Without thorough cleaning, the space may fail inspection due to safety or hygiene violations. Specialty cleaning companies understand the documentation and procedures required to meet both internal standards and regulatory guidelines.
Facility managers should note that specialty cleaners often provide checklists and reports documenting what was cleaned, how it was cleaned, and what methods were used. This documentation is valuable when transitioning a construction project to operational status, particularly in industries with strict inspection protocols. Relying on general janitorial providers can lead to delays or rework due to missed cleaning targets.
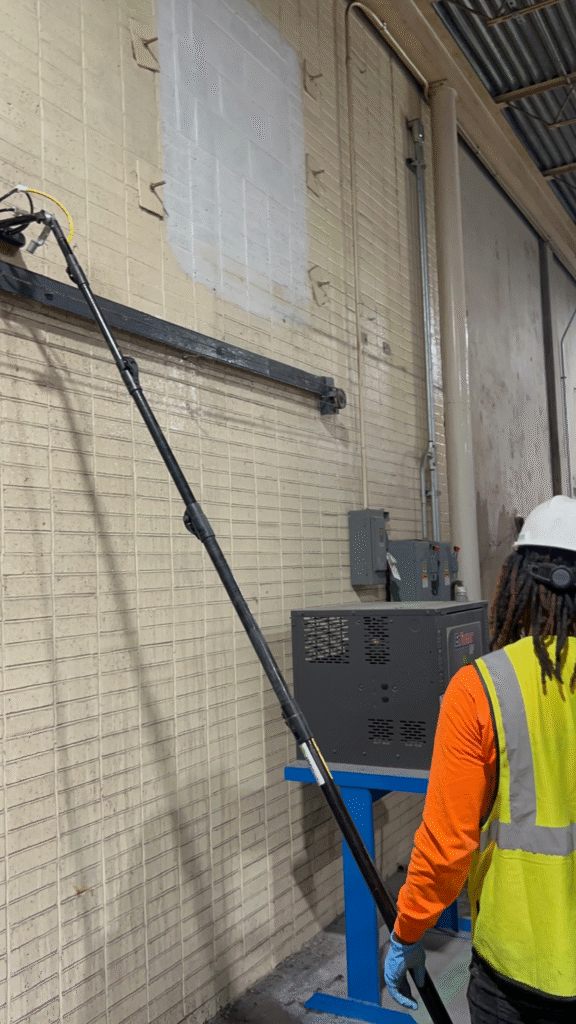
Specialized Equipment Makes the Difference
It’s not just about having a mop and broom. Specialty post-construction cleaning teams bring commercial-grade equipment and supplies, including high-suction vacuums, pressure washers, and industrial scrubbers. These tools are designed for deep cleans and can remove substances that traditional janitorial tools cannot.
Moreover, cleaning teams trained in construction site safety are better prepared to work around newly installed features and avoid damage. Their training also reduces the risk of workplace accidents during the cleaning phase—an essential concern for facility managers responsible for a safe handover.
Why the Right Cleaning Partner Matters
For commercial developers and facility managers in Kansas and Missouri, post-construction cleanup is not the stage to cut corners. It’s the bridge between project completion and business readiness. Whether managing distribution facilities or commercial buildings, the right partner understands how to transform a construction zone into a clean, functional, and code-compliant workspace.
Choosing a commercial cleaning company in Kansas City that understands the unique demands of post-construction environments can streamline project closeout and prevent operational setbacks. Services that also specialize in floor care solutions in Lees Summit, MO, and building maintenance services in Kansas City ensure continuity in facility upkeep beyond the initial cleanup phase.
To make sure your space is truly ready for occupancy—beyond what a standard janitorial crew can offer—reach out to Crystal Clear Enterprise. Their expert teams provide industry-focused, post-construction cleaning services that meet the standards of safety, durability, and professional presentation.
Contact them today.
About the Author:
Taylor Greene is a facilities consultant with over 12 years of experience working with manufacturing and commercial real estate clients across the Midwest. She regularly writes about building maintenance standards, compliance practices, and innovations in commercial cleaning. Her focus is on helping organizations maintain efficiency and safety through proper facility care. Taylor is passionate about operational integrity and writes to inform professionals responsible for workplace quality and compliance.