Choosing the Right Hydraulic Fittings for Your System
Hydraulic fittings are an essential component in fluid power systems, responsible for connecting hoses, pipes, and tubes to control the...
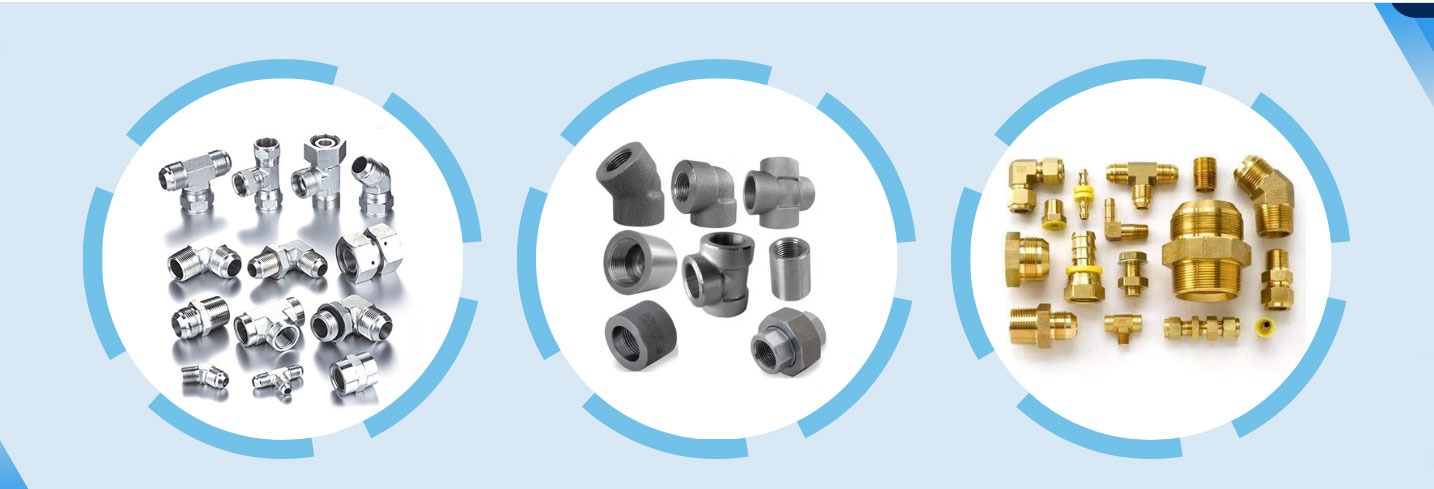
Hydraulic fittings are an essential component in fluid power systems, responsible for connecting hoses, pipes, and tubes to control the flow of fluid and ensure the system operates efficiently and reliably. Whether you’re dealing with machinery, industrial systems, or automotive applications, choosing the right hydraulic fittings is critical for system performance, safety, and longevity. In this guide, we will explore expert tips and insights on selecting the appropriate hydraulic fittings, emphasizing the importance of understanding their types, sizes, materials, and other key factors.
Understanding Hydraulic Fittings
Hydraulic fittings play a crucial role in hydraulic systems. They are designed to join tubes, hoses, and pipes with hydraulic components, ensuring the flow of hydraulic fluid is controlled. Without these fittings, a hydraulic system would be ineffective, resulting in leaks, pressure drops, and even complete system failure. These fittings are available in various designs, materials, and sizes, allowing you to customize your system according to specific requirements.
Before we dive into the factors that influence the selection of hydraulic fittings, let’s explore the different types available:
Types of Hydraulic Fittings
There are several types of hydraulic fittings, each suited for specific applications. Here are some of the most common:
- Threaded Hydraulic Fittings Threaded fittings are commonly used in hydraulic systems. These fittings use threads to create a seal and secure the connection between two parts. They are available in a range of thread types, including NPT (National Pipe Thread), BSP (British Standard Pipe), and JIC (Joint Industrial Council).
- Flared Hydraulic Fittings Flared fittings are designed with a cone-shaped flare at the end of the pipe or tube. This flare creates a seal when the fitting is tightened, making them ideal for high-pressure applications.
- Compression Fittings Compression fittings are used to join two tubes or pipes by compressing the tube inside the fitting, creating a tight seal. These are ideal for smaller systems and can be used for both low and high-pressure applications.
- Push-to-Connect Hydraulic Fittings Push-to-connect fittings are easy to install and require no tools. They are often used in applications where quick disconnection and reconnection are necessary. They are commonly found in mobile machinery and automotive systems.
- Banjo Fittings Banjo fittings are used when space is limited. These fittings feature a hollow design that allows fluid to flow through while maintaining a compact connection.
Each type of hydraulic fitting has its own strengths and weaknesses, and understanding their applications is crucial for selecting the right one for your system.
Key Factors to Consider When Choosing Hydraulic Fittings
Choosing the right hydraulic fitting goes beyond simply selecting a type. Several factors influence the decision-making process, including pressure ratings, material compatibility, and size. Let’s explore these factors in more detail.
1. Pressure Rating and System Specifications
Pressure is a critical factor in any hydraulic system. Hydraulic fittings must be able to withstand the pressures exerted by the system without failing. Each fitting is designed to handle a specific pressure range, and it’s essential to select fittings that match your system’s pressure requirements.
When choosing hydraulic fittings, always check the maximum working pressure rating. This information is typically provided by the manufacturer and indicates the maximum pressure the fitting can handle without risk of failure. Be sure to consider both the pressure at peak load and the sustained pressure during normal operation.
2. Material Compatibility
The material used in the hydraulic fitting is another essential consideration. Hydraulic fittings are typically made from materials such as steel, stainless steel, brass, aluminum, or plastic. The material choice impacts the fitting’s durability, resistance to corrosion, and ability to withstand high temperatures and pressures.
- Steel is the most common material used for hydraulic fittings due to its strength and durability.
- Stainless steel offers superior resistance to corrosion and is ideal for harsh environments.
- Brass is corrosion-resistant and often used in low-pressure systems.
- Aluminum is lightweight and ideal for systems where weight is a concern.
- Plastic fittings are often used for low-pressure applications or where flexibility is needed.
It’s crucial to choose hydraulic fittings that are compatible with the material of your hydraulic system, including hoses, tubes, and components. For example, if you are using a stainless steel hose, you should select stainless steel hydraulic fittings to ensure a proper seal and prevent corrosion.
3. Size and Compatibility
Size is another vital factor to consider when selecting hydraulic fittings. The size of the fitting must match the size of the pipe, hose, or tube being used in the system. If the fitting is too large or too small, it will not form a proper seal, leading to leaks or system failure.
Most hydraulic fittings come in standard sizes, such as 1/4″, 1/2″, 3/4″, and 1″, but it’s essential to check the exact dimensions before making a purchase. In addition, make sure to account for the fittings’ compatibility with other components in your system, including seals, threads, and pressure ratings.
4. Temperature Range
Hydraulic systems often operate in environments with extreme temperatures. Choosing hydraulic fittings that can withstand the temperatures in your system is crucial for ensuring reliable operation. Be sure to verify the temperature range of the hydraulic fittings you select and ensure they match the operational temperatures of your system.
For instance, if your system operates in high-temperature conditions, stainless steel or brass fittings may be the best option as they offer better heat resistance than plastic fittings.
5. Seal Types
The seal type is a critical consideration when selecting hydraulic fittings. A poor seal can lead to leaks and inefficiency in the system. There are several types of seals commonly used in hydraulic fittings, including:
- O-Rings: O-rings are one of the most common sealing methods. They create a tight seal between two surfaces and are available in various materials, including rubber, Viton, and polyurethane.
- Metal-to-Metal Seals: These seals are often used in high-pressure applications where a more durable and long-lasting seal is required.
- Face Seals: Face seals use a flat metal surface to create a seal, and they are often used in applications with high flow rates.
Ensure that the seal type matches the fluid, pressure, and temperature specifications of your system.
6. Environmental Considerations
The environment in which your hydraulic system operates also impacts your choice of hydraulic fittings. If your system is exposed to harsh chemicals, high temperatures, or abrasive conditions, you may need specialized hydraulic fittings made from materials like stainless steel or corrosion-resistant alloys.
Additionally, consider the risk of contamination in your hydraulic fluid. For systems in dirty or hazardous environments, consider using hydraulic fittings that feature built-in filters or seals to prevent contaminants from entering the system.
How to Maintain Hydraulic Fittings for Optimal Performance
Proper maintenance of hydraulic fittings is essential for ensuring their longevity and continued efficiency. Here are some tips to keep your hydraulic fittings in top condition:
- Regular Inspections: Periodically check for leaks, cracks, or signs of wear and tear. Replace damaged fittings immediately to avoid system failure.
- Proper Installation: Always follow manufacturer guidelines for installation to ensure the fittings are properly sealed and tightened.
- Cleanliness: Keep hydraulic fittings clean and free of debris, which can cause blockages or contamination in the system.
- Lubrication: Use the recommended lubricants for hydraulic fittings to ensure smooth operation and prevent friction-related damage.
Common Hydraulic Fittings Issues and How to Resolve Them
Even with proper selection and maintenance, hydraulic fittings can sometimes encounter problems. Here are some common issues and how to address them:
- Leaks: If you notice fluid leaking from a hydraulic fitting, it could be due to improper installation, worn seals, or damaged threads. Check the fitting’s alignment and replace any worn seals.
- Loose Connections: Over time, hydraulic fittings can loosen due to vibrations or thermal expansion. Tighten connections periodically to prevent this issue.
- Corrosion: Corrosion can degrade the fitting material and lead to system failure. Ensure that your fittings are made from corrosion-resistant materials or are treated with anti-corrosion coatings.
Conclusion
Selecting the right hydraulic fittings is crucial for ensuring the optimal performance and longevity of your hydraulic system. Whether you’re dealing with pressure requirements, material compatibility, or size specifications, the right fitting can make all the difference in your system’s efficiency and reliability. By considering factors such as pressure ratings, material properties, and seal types, you can choose the best hydraulic fittings for your system and avoid common issues such as leaks, pressure drops, and equipment failure.
Make sure to consult with experts and carefully follow installation and maintenance guidelines to keep your hydraulic system running smoothly. By making informed choices, you can ensure the continued success of your hydraulic applications and avoid unnecessary downtime or repairs.