Boost Productivity with a Desktop Laser Welding Machine
In today’s fast-paced manufacturing environment, staying competitive means finding ways to increase efficiency without compromising quality. Whether you’re a small...
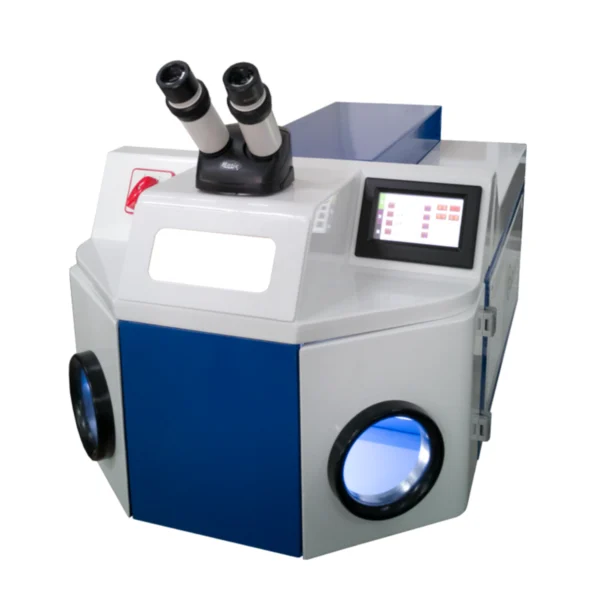
In today’s fast-paced manufacturing environment, staying competitive means finding ways to increase efficiency without compromising quality. Whether you’re a small workshop or a growing industrial business, investing in the right tools can dramatically impact your workflow. One such tool making waves across industries is the desktop laser welding machine. Compact, precise, and highly effective, this device can significantly boost productivity while maintaining superior quality standards.
Compact Size, Maximum Flexibility
One of the most notable advantages of desktop laser welders is their compact form factor. Unlike traditional welding machines, which often require significant space and setup, a desktop laser welder fits easily on a workbench or small workstation. This makes it an ideal solution for small businesses, hobbyists, or companies with limited floor space.
Despite their size, these machines offer impressive flexibility. They can weld a wide range of materials, including stainless steel, carbon steel, aluminum, titanium, and even dissimilar metals. This makes them suitable for diverse applications—from jewelry making and dental work to electronics and automotive components.
Speed and Precision in Every Weld
Laser welding is known for its unmatched precision and speed. Traditional welding methods can leave behind large heat-affected zones, leading to warping or damage to sensitive parts. Desktop laser welders, on the other hand, focus energy so precisely that they minimize heat distribution, resulting in cleaner welds and reduced need for post-processing.
The laser beam’s pinpoint accuracy allows operators to create strong, seamless joints in even the most delicate components. This translates to fewer errors, less material waste, and more consistent results across projects—all of which directly contribute to increased productivity.
Minimal Setup and Training Required
Ease of use is another critical factor that boosts workplace efficiency. Desktop laser welders often come with user-friendly interfaces, intuitive controls, and pre-set parameters for common materials and thicknesses. This reduces the learning curve for new operators and allows teams to hit the ground running.
Many models also feature plug-and-play capabilities, meaning you can set up and start welding with minimal downtime. There’s no need for elaborate preparation or specialized environments—just connect, calibrate, and start working.
Reduced Downtime and Maintenance
Downtime is the enemy of productivity. Traditional welding methods often involve consumables like filler materials, electrodes, or shielding gases, all of which can deplete quickly and interrupt workflow. Laser welders eliminate many of these needs. Since they often rely solely on concentrated laser beams, consumables are minimal or non-existent.
Additionally, these machines have fewer moving parts, which means reduced wear and tear. This leads to lower maintenance requirements, fewer interruptions, and more time spent getting actual work done.
Enhanced Safety and Cleanliness
Workplace safety is a major concern, especially in environments where heat, sparks, and fumes are involved. Desktop laser welding machines offer a safer alternative to traditional methods. Many models come with enclosures or shielding to protect the operator from the laser beam, and they produce significantly fewer fumes and sparks.
A cleaner, safer work environment not only protects workers but also contributes to more efficient operations. You won’t need to invest as much time in cleaning up or implementing additional safety measures, allowing for a more streamlined workflow.
Ideal for Small Batch and Custom Work
For businesses that handle custom or low-volume production runs, desktop laser welders are especially valuable. They provide the flexibility to make quick changes, switch between different types of materials, and perform detailed work without having to retool the entire production line.
This adaptability is key in markets where customization, precision, and fast turnaround times are in high demand. Whether you’re welding custom frames, intricate metal art, or precision electronic components, laser welding offers the versatility to get the job done efficiently.
Long-Term Cost Savings
While the upfront cost of a desktop laser welding machine may be higher than traditional alternatives, the long-term savings are substantial. Reduced material waste, lower energy consumption, minimal maintenance, and faster production all contribute to a lower cost per weld over time.
Furthermore, the improved quality of welds means fewer rejects and reworks, which can significantly cut costs in the long run. As a result, the return on investment for desktop laser welders is often realized much faster than expected.
Conclusion
In a competitive manufacturing landscape, tools that enhance productivity without sacrificing quality are invaluable. A desktop laser welding machine delivers on all fronts: it’s compact, efficient, precise, and easy to use. Whether you’re looking to increase output, reduce errors, or simply create a cleaner and safer workspace, laser welding technology can provide the edge your business needs to succeed.