A Guide to Stacking Modules in Automation Systems
In the world of modern automation and industrial robotics, efficiency, modularity, and space optimization are key performance indicators that drive...
In the world of modern automation and industrial robotics, efficiency, modularity, and space optimization are key performance indicators that drive successful production outcomes. One critical yet often overlooked component enabling these advancements is the stacking modules used in various automated systems. These modules play a central role in facilitating structured, scalable, and efficient automation setups, especially in environments where precision, speed, and spatial economy are crucial.
Whether it’s a robotic assembly line moving fragile food products or a high-precision operation processing micro-optical components, the structure of the automation system has to be adaptable, reliable, and efficient. This is exactly where stacking modules becomes essential.
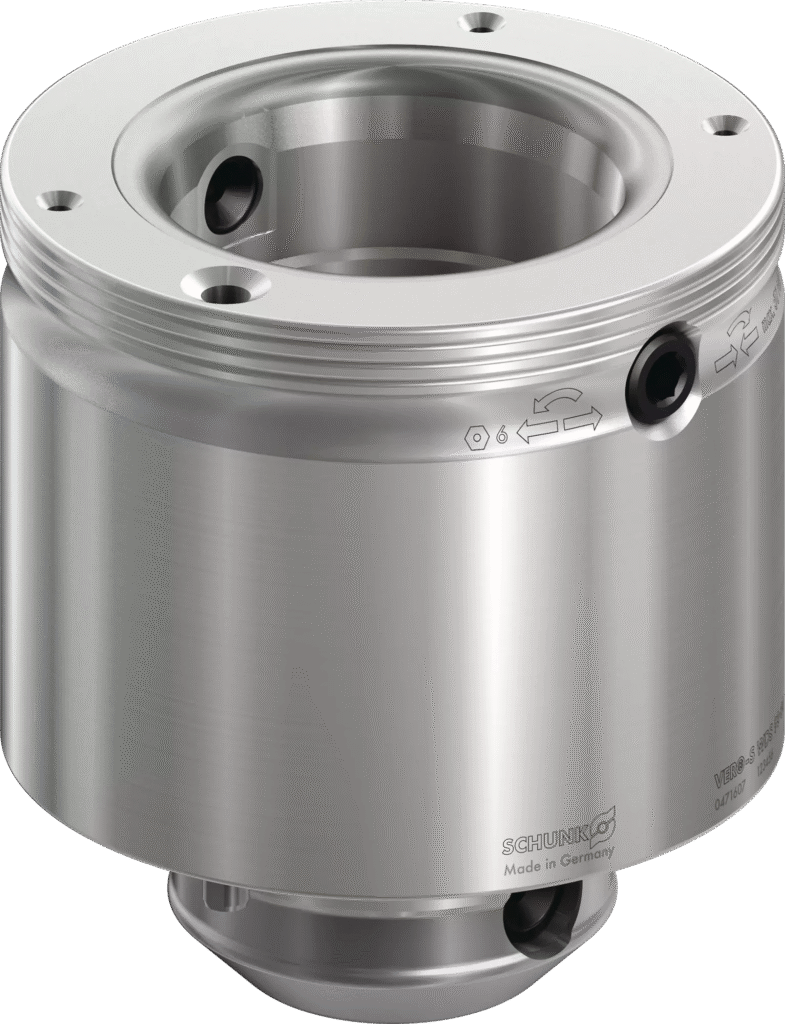
What Are Stacking Modules?
Stacking modules are modular units used to support the layered or sequential assembly of mechanical, pneumatic, or robotic systems. These modules enable multiple functions to be integrated vertically or horizontally without occupying additional floor space or requiring extensive modifications to existing machinery.
Each module performs a specific function, such as gripping, positioning, clamping, or rotating, and can be combined with others to form a flexible structure. This modular approach is especially useful in automated manufacturing systems, where custom setups are frequently required to adapt to different products, batch sizes, or processes.
Role of Stacking Modules in Automation
In industrial automation, consistency and adaptability are top priorities. Stacking modules support these goals by enabling:
Compact Design: They allow various functional elements to be layered within a limited footprint.
Functional Integration: Multiple modules can perform different operations in one unified system.
Customizability: Easy to reconfigure according to different production needs.
Time Savings: Reduced system assembly time with modular plug-and-play setups.
Improved Maintenance: Faulty units can be replaced or upgraded without dismantling the entire system.
In production processes involving frequent changes in tooling, workpieces, or batch sizes, these benefits significantly enhance operational flexibility.
Applications of Stacking Modules
Stacking modules are found in a wide range of sectors that require high-speed, precise automation. Here are some notable use cases:
Packaging and Handling
Modules can be stacked to execute sequential operations like picking, placing, rotating, and pushing—ideal for handling fragile items such as butter cookies or consumer electronics.
Assembly Lines
Stacking modules helps organize multiple tooling or gripper functions in one compact unit, which is particularly useful in assembling automotive or electronic components.
Medical Equipment Manufacturing
In applications like milling hip implants, precision and cleanliness are vital. Stacking modules allows seamless transitions between tools and operations in a controlled, compact space.
Optical Component Processing
Micro-optics require stable, vibration-free movements. Stacking configurations can isolate vibration while managing complex positioning tasks, helping maintain ultra-high precision.
These examples show how stacking modules serve as structural and functional backbones for diverse automated systems, regardless of the industry.
Key Features and Benefits of Stacking Modules
Stacking modules offer features that make them indispensable in advanced manufacturing setups:
Space Efficiency
With space often at a premium, especially in clean rooms or compact production areas, stacking reduces horizontal sprawl and maximizes vertical space.
Enhanced Modularity
Different modules for clamping, rotating, lifting, or pushing can be assembled as needed, enabling tailored systems for complex or evolving processes.
Compatibility with Pneumatic and Electric Systems
They can integrate with various drive technologies, making them suitable for both traditional pneumatic systems and modern servo-controlled setups.
Quick Changeover Capabilities
Operators can quickly swap modules without tools, reducing downtime and allowing fast adaptation to changing production requirements.
Simplified Maintenance
Modular designs mean that a faulty module doesn’t halt the entire operation. It can be individually accessed and replaced without dismantling the full assembly.
These attributes contribute significantly to increased uptime, better control, and optimized throughput in automated systems.
Read also: A Complete Guide to Industrial Robotics and Automation Systems
Integrating Stacking Modules with Robotic Systems
The modular nature of stacking modules makes them a perfect match for robotic systems that require both flexibility and precision. In typical industrial robotic applications, stacking modules may support:
Grippers for delicate material handling
Rotating units for part orientation
Linear actuators for vertical movement
Clamping devices to secure workpieces during secondary processes
Each unit is designed to operate either independently or in conjunction with the others, forming an intelligent, synchronized automation cell. This approach helps create modular end-of-arm tooling systems, where robotic arms can switch between different modules depending on the task at hand.
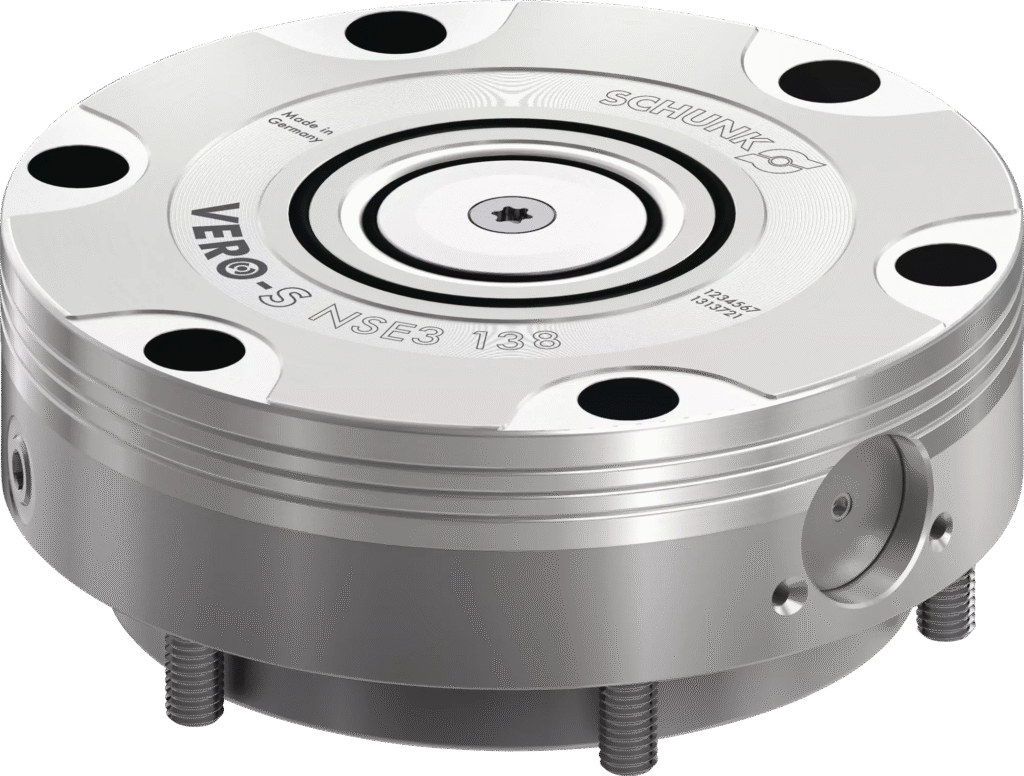
Flexibility and Customization through SCHUNK Products
In the field of automation and robotic integration, product adaptability plays a vital role. High-quality modular components are essential for scalable, long-lasting automation systems.
Schunk products, known for their durability and engineering precision, offer a complete suite of components suitable for stacking configurations. From pneumatic grippers and rotary modules to intelligent toolholding and clamping solutions, SCHUNK’s modular offerings simplify complex tasks.
The compatibility between SCHUNK grippers and actuators allows multiple modules to be integrated in a compact yet powerful setup. Whether it’s handling micro-sized components or large-scale industrial parts, SCHUNK products support high reliability and seamless scalability.
Engineered with clarity and precision, SCHUNK products embody decades of experience, rigorous quality control, and customer-focused development. The modules are designed to integrate easily, reduce complexity, and enhance overall system performance — a key requirement in any forward-looking automation project.
Future of Automation with Modular Integration
As production needs continue to shift toward customization, smaller batch sizes, and faster delivery times, the demand for modular, reconfigurable automation systems will grow. In this evolving environment, stacking modules will play a central role in ensuring that automated processes are flexible, responsive, and efficient.
By enabling easy integration, modularity, and compact design, these modules help meet the requirements of a highly dynamic industrial world, from processing hair-thin optical parts to handling large-scale assemblies with multiple coordinated movements.
Conclusion
The foundation of any successful automation system lies in its ability to adapt and perform consistently under changing conditions. Stacking modules provide this adaptability, offering structural and functional versatility that helps manufacturers optimize space, reduce downtime, and improve efficiency.
In today’s competitive environment, where precision and reliability are essential, companies need partners they can trust. With decades of expertise, unwavering commitment to quality, and a forward-thinking approach to automation, SCHUNK delivers modular solutions that empower manufacturers to build systems tailored to their unique challenges. Whether you are scaling production, improving flexibility, or simplifying operations, SCHUNK provides the technology and reliability to help you move forward.