A Complete Guide to Choosing the Right Lathe Machine Chuck
In the world of machining, precision and efficiency go hand in hand. The right tools can make a significant difference...
In the world of machining, precision and efficiency go hand in hand. The right tools can make a significant difference in both productivity and product quality. One such essential component in any turning operation is the lathe machine chuck. Whether you’re a workshop owner, a machinist, or an engineer, understanding the fundamentals and types of lathe chuck systems can help you make informed choices that lead to better machining results.
This comprehensive guide dives into everything you need to know about choosing the right lathe machine chuck—from types and materials to applications and buying tips.
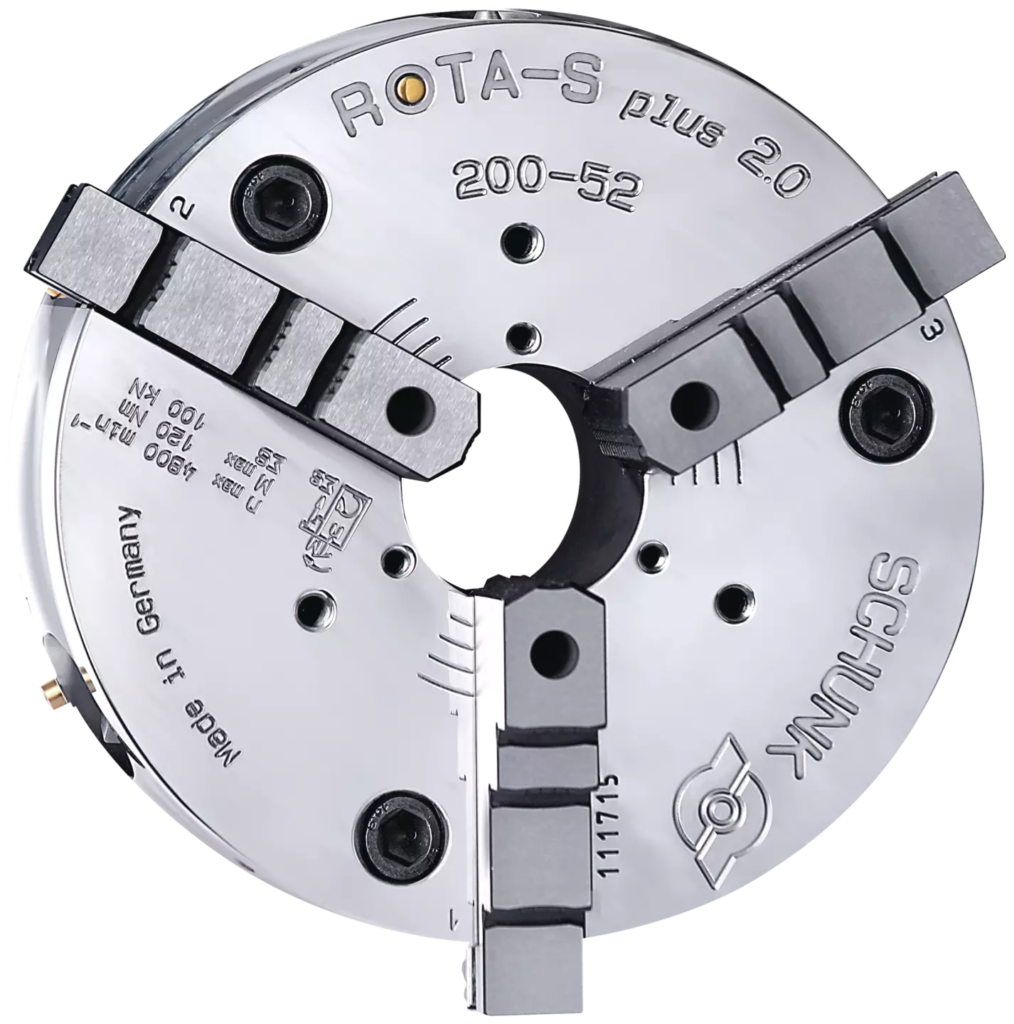
What is a Lathe Machine Chuck?
A lathe machine chuck is a specialized clamping device attached to the spindle of a lathe. Its main function is to hold the workpiece tightly and precisely as it rotates. Chucks come in various shapes, sizes, and jaw configurations, designed for different types of turning operations.
The efficiency, accuracy, and versatility of your lathe depend significantly on the lathe chuck you choose. Selecting the wrong chuck may lead to errors, workpiece slippage, and even equipment damage.
Importance of Choosing the Right Lathe Chuck
Choosing the appropriate lathe chuck isn’t just about compatibility—it impacts:
Machining accuracy
Workpiece stability
Operator safety
Tool life
Setup and cycle times
With increasing demands in industries like aerospace, automotive, and precision engineering, the need for the right lathe machine chuck has never been greater.
Types of Lathe Machine Chucks
Here are the most common types of lathe chucks, along with their features and ideal applications:
Three-Jaw Self-Centering Chuck
Commonly Used For: Cylindrical or symmetrical workpieces
Operation: All three jaws move simultaneously
Advantages:
Quick setup
Suitable for most general-purpose turning
Limitations:
Less accuracy compared to independent chucks
This type of lathe machine chuck is ideal for fast production environments where precision is not the highest priority.
Four-Jaw Independent Chuck
Commonly Used For: Irregular shapes or off-center workpieces
Operation: Each jaw moves independently
Advantages:
High accuracy
Adjustable for complex shapes
Limitations:
Slower setup
Requires more skill to align the workpiece
Four-jaw lathe chucks are highly versatile, making them a favorite in custom machining jobs.
Collet Chuck
Commonly Used For: Small, high-precision workpieces
Operation: Uses a collet (a sleeve that forms a collar)
Advantages:
Superior grip
High RPM capability
Limitations:
Limited to specific sizes
Higher cost for multiple collet sizes
Ideal for CNC lathes and applications requiring consistent precision, such as watchmaking or electronics manufacturing.
Magnetic Chuck
Commonly Used For: Ferromagnetic workpieces
Operation: Uses magnetic force to hold the workpiece
Advantages:
No mechanical pressure on the workpiece
Even holding pressure
Limitations:
Only suitable for magnetic materials
Not ideal for heavy-duty operations
This lathe machine chuck is beneficial in grinding and light turning tasks.
Hydraulic and Pneumatic Chucks
Commonly Used For: Automated production lines
Operation: Uses fluid or air pressure to clamp
Advantages:
High clamping force
Fast and automatic operation
Limitations:
Complex system
Higher initial investment
These chucks are essential in high-volume, automated environments such as automotive manufacturing.
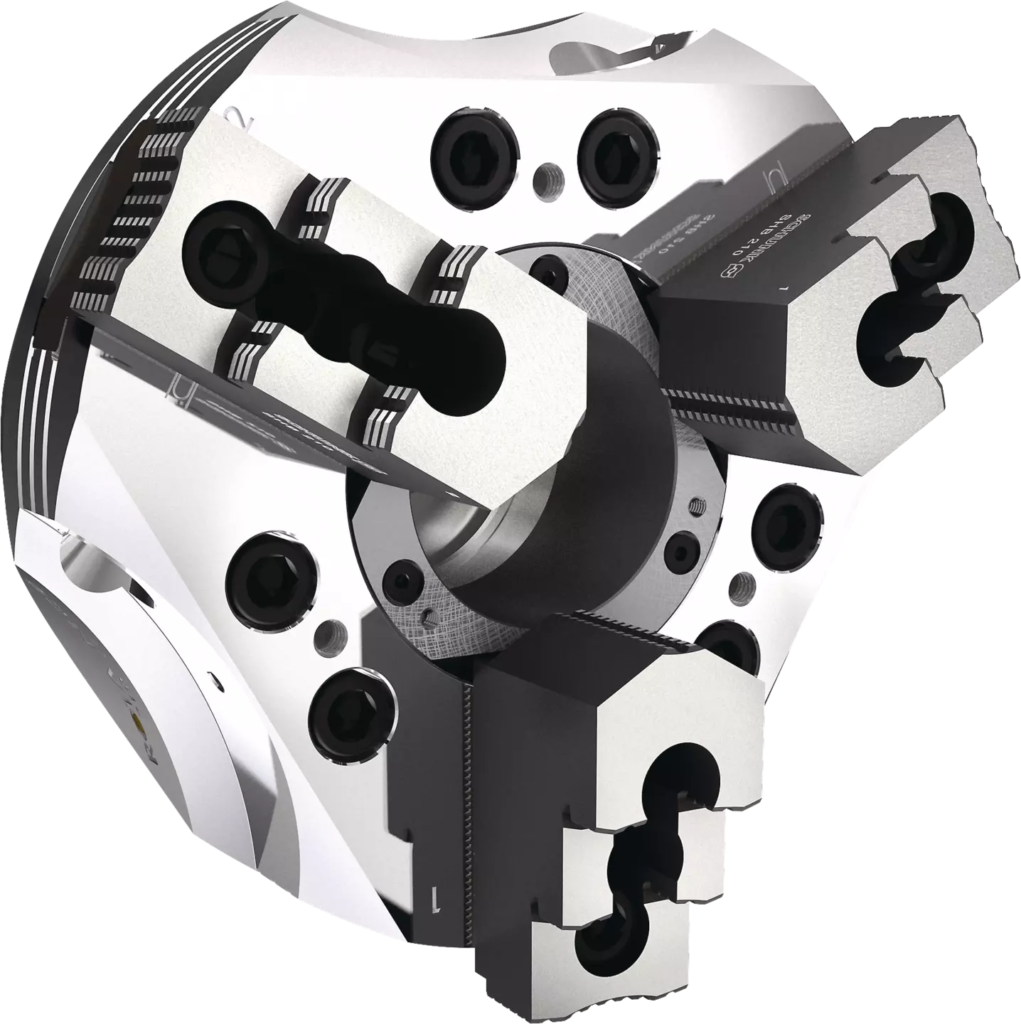
Key Factors to Consider When Choosing a Lathe Machine Chuck
Selecting the right lathe chuck involves evaluating multiple factors based on your specific use case:
Workpiece Shape and Size
Consider whether you’re turning round, square, or irregularly shaped materials. While three-jaw chucks are ideal for round parts, four-jaw independent chucks are better for odd shapes.
Material Type
The hardness and machinability of the workpiece material influence the type of chuck needed. Magnetic chucks, for instance, are only suitable for ferrous materials.
Precision Requirements
For high-accuracy operations, collet chucks or four-jaw independent chucks are more appropriate. Self-centering chucks may suffice for lower tolerance needs.
Machine Compatibility
Ensure the chuck fits your lathe spindle—consider mounting type, chuck diameter, and operating speed (RPM).
Clamping Force
Different materials and operations require different levels of clamping force. Hydraulic chucks offer more consistent and powerful clamping.
Production Volume
For high-speed production, opt for chucks that offer faster changeovers, such as quick-change or automated models.
Budget and Maintenance
Some chucks are cost-effective upfront but require frequent maintenance, while others have a higher initial cost but offer better longevity and lower maintenance needs.
Latest Innovations in Lathe Chuck Technology
The evolution of smart manufacturing and the lathe machine chuck industry has led to several technological advancements:
Sensor-Integrated Chucks: These monitor clamping force and tool wear in real-time.
Quick-Change Systems: Allow for rapid chuck jaw swaps, minimizing downtime.
Lightweight Chucks: Reduce rotational inertia, saving energy and increasing RPM capability.
Automated Chucks: Integrate seamlessly with robotic arms and CNC systems.
These innovations are becoming increasingly popular within the broader lathe chuck market, especially in sectors embracing Industry 4.0 principles.
Tips for Maintaining Your Lathe Chuck
Once you’ve selected the right lathe machine chuck, proper maintenance ensures peak performance and longevity:
Regular Cleaning: Remove chips, dirt, and coolant residues after each use.
Lubrication: Grease moving parts according to the manufacturer’s schedule.
Jaw Calibration: Periodically check and re-center jaws for accuracy.
Visual Inspection: Look for signs of wear, cracks, or deformation.
Test Clamping Force: Make sure the chuck maintains adequate grip under load.
Neglecting chuck maintenance can result in poor surface finish, safety hazards, and reduced tool life.
Common Mistakes to Avoid
Choosing the Wrong Jaw Type: Always match jaw types with your workpiece geometry.
Ignoring Balance at High Speeds: Unbalanced chucks at high RPM can damage both the machine and the workpiece.
Using One Chuck for All Tasks: Special applications often need specialized chucks—don’t compromise on performance.
Over-tightening: Excessive force can damage soft materials or deform the workpiece.
Conclusion
Choosing the right lathe machine chuck is a critical decision that impacts every aspect of your machining operation—from precision and productivity to tool life and worker safety. As the demand for precision manufacturing continues to grow, so does the need for reliable, high-quality lathe chucks.
One of the most trusted names in the field of clamping and gripping technology is Schunk. Renowned for their German engineering excellence, Schunk offers a wide range of lathe chucks and clamping systems designed for high-performance, precision machining. Whether you’re in aerospace, automotive, or general manufacturing, Schunk provides innovative and durable chucking solutions that align with the evolving demands of modern machining.
Investing in the right lathe machine chuck is more than just a technical decision—it’s a strategic move toward better performance, lower operational costs, and superior product quality.