Unlocking Industrial Efficiency: Why the Liquid Ring Vacuum Pump Remains an Unmatched Solution
In the evolving world of industrial vacuum era, the liquid ring vacuum pump has earned a stable reputation for its...
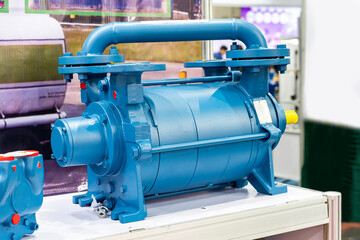
In the evolving world of industrial vacuum era, the liquid ring vacuum pump has earned a stable reputation for its reliability, sturdiness, and adaptability across a huge variety of applications. Known for its capacity to handle wet, dry, and corrosive gases, this strong pump continues to be a cornerstone of vacuum technology in industries as various as chemical processing, pharmaceuticals, food production, pulp and paper, and electricity era.
At its middle, the liquid ring vacuum pump operates on an easy yet notably effective principle. Its layout permits continuous, non-pulsating suction, making it perfect for methods that demand solid vacuum conditions underneath hard operational environments. While various vacuum technologies have emerged over time, the liquid ring pump stays a desired choice because of its specific benefits in managing process gases that comprise moisture or contaminants.
Its relevance in latest commercial weather is in addition bolstered with the aid of its compatibility with environmentally conscious practices and sustainability dreams. As industries location more emphasis on procedure performance and lengthy-time period reliability, vacuum structures powered by way of liquid ring generation maintain to set the same old.
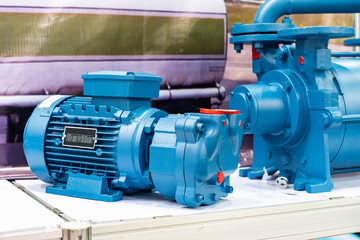
Understanding the Working Principle of Liquid Ring Technology
The operation of a liquid ring vacuum pump is based on a trustworthy mechanism involving centrifugal pressure and a sealing liquid—normally water or other compatible fluids. Inside the pump casing, an eccentrically mounted impeller rotates at excessive pace. As it spins, the sealing liquid is thrown outward by way of centrifugal pressure to form a ring alongside the internal wall of the pump casing. This liquid ring creates a chain of enclosed spaces among the impeller blades.
As the impeller maintains to rotate, the volume of those areas adjustments cyclically. On the suction facet of the pump, the extent between the blades increases, drawing in gas or vapor from the system. As the impeller rotates in the direction of the release facet, the quantity decreases, compressing the gasoline and forcing it out of the pump.
This method allows the pump to deal with massive volumes of gas with minimum mechanical wear, because the running fluid additionally acts as a lubricant and a cooling agent. Because the pump does now not depend on internal contact between moving parts and the casing, it operates easily and with less friction, making it mainly appropriate for non-stop-responsibility programs.
Applications Across Diverse Industries
The versatility of liquid ring vacuum pumps is a first-rate component of their sizeable use across global industries. They are particularly nicely-ideal for processes in which moisture-laden gases are not unusual, or wherein the vacuum machine should accommodate unexpected surges in vapor or gas go with the flow.
In the chemical and pharmaceutical sectors, those pumps are used for solvent healing, distillation, crystallization, and vacuum filtration. Their ability to tolerate condensable vapors and corrosive substances with out performance degradation makes them quintessential in sensitive technique environments.
In meals and beverage processing, they are commonly hired for degassing, vacuum packing, and concentrating products. The pump’s hygienic design, mixed with its capacity to preserve steady vacuum stages, enables ensure each product best and technique performance.
Power era centers make use of liquid ring pumps for condenser air extraction and vacuum priming of structures. Their ability to address saturated gases and occasional liquid carryover with out harm makes them ideal for these demanding packages.
In pulp and paper production, liquid ring pumps assist dewatering, vacuum forming, and different ranges of the paper-making procedure, contributing to higher manufacturing throughput and decreased energy intake.
Advantages of the Liquid Ring Design
What makes the liquid ring vacuum pump this kind of reliable option is its rugged design and operational flexibility. These pumps are inherently tolerant of beverages and particulates in the gasoline circulate, which offers them a good sized advantage over dry vacuum systems in positive environments.
Because the pump’s internal components are continuously cooled and lubricated through the sealing fluid, it reviews decrease put on and may maintain green operation over prolonged durations. Additionally, the design gets rid of the want for complicated valves, diaphragms, or tight clearances, lowering the risk of mechanical failure.
Another advantage is the pump’s potential to control fluctuating loads without fundamental performance losses. Processes that contain sudden stress adjustments or varying gasoline compositions can run greater smoothly with liquid ring pumps, which adapt naturally to the ones adjustments.
From an acoustic perspective, those pumps are particularly quiet at some point of operation, contributing to safer and more snug paintings environments. And in view that they use water or well suited system fluids as sealing dealers, they’re a realistic choice for operations seeking non-oil vacuum answers.
Configurations and System Integration
Liquid ring vacuum pumps are available single-level and -level configurations, relying at the application necessities. Single-stage pumps are perfect for applications requiring slight vacuum degrees, normally down to around 30 mbar. Two-degree models are designed for deeper vacuum packages and may gain pressures under 10 mbar whilst nevertheless handling vapors effectively.
The choice of sealing liquid also performs a important function in overall performance. While water is maximum normally used, specific techniques might also require natural fluids or chemical substances to save you contamination or enhance compatibility with system gases. In closed-loop structures, sealing liquid is recovered, cooled, and recirculated, which improves performance and minimizes waste.
System designers frequently integrate those pumps with separators, warmness exchangers, and restoration tanks to optimize fluid usage and ensure smooth operation. Advanced control structures now allow real-time monitoring of pump overall performance, fluid levels, and operational parameters—supporting centers keep uptime and preemptively cope with protection desires.
Collaborating with knowledgeable vacuum producers for the duration of machine layout and set up ensures that those integration options are tailored to meet each performance and sustainability goals.
Energy Consumption and Environmental Considerations
One of the worries traditionally associated with liquid ring vacuum pumps is their water intake, specially in as soon as-thru systems. However, modern-day installations often utilize closed-loop configurations to minimize water utilization and environmental impact. In those systems, the sealing liquid is reused after passing via a cooling stage, drastically lowering water waste and running costs.
Energy efficiency is every other place where upgrades were made. By optimizing internal geometries, upgrading force structures, and using variable velocity drives, manufacturers have succeeded in making more moderen liquid ring pumps some distance extra energy-efficient than preceding generations.
From an emissions point of view, those pumps excel at taking pictures and managing vapors that might in any other case be released into the surroundings. Their capacity to condense and get better valuable method vapors now not simplest reduces emissions however also complements material recovery and technique economics.
By combining those environmental and financial blessings, liquid ring pumps are increasingly more being aligned with green production dreams, company sustainability efforts, and compliance with regulatory frameworks.
Maintenance and Operational Longevity
Maintenance simplicity is an indicator of liquid ring vacuum pumps. The design lacks complicated internal elements that require common service, and the usage of sealing fluid protects inner surfaces from corrosion and fouling. Basic preservation generally involves tracking fluid first-rate, checking for leaks, and inspecting seals and bearings at scheduled periods.
Sealing liquid contamination can from time to time arise if manner gases comprise aggressive chemical substances or particulates. In such instances, filtration structures and normal fluid substitute assist maintain pump performance. Pumps used in harsh chemical environments can be synthetic with corrosion-resistant substances which include stainless steel or specialised coatings to increase carrier life.
With proper upkeep, those pumps can stay operational for years with minimal downtime. Their resilience, combined with reliable performance, makes them an great lengthy-term funding in business systems where reliability is paramount.
Emerging Technologies and Future Prospects
As the vacuum industry evolves, liquid ring pump technology isn’t always standing nonetheless. Innovations in computational fluid dynamics (CFD) have allowed for more efficient impeller and housing designs, optimizing float traits and decreasing energy needs. These layout upgrades make a contribution to each higher throughput and progressed vacuum balance.
Manufacturers also are exploring methods to lessen environmental impact further, along with integrating clever monitoring equipment for predictive preservation and electricity control. Some more moderen models contain corrosion-resistant alloys and green sealing fluids to higher meet the demands of modern-day manufacturing and processing environments.
Hybrid systems that integrate liquid ring pumps with other vacuum technologies, together with dry screw or rotary vane gadgets, are gaining popularity in industries where a extensive operating variety is required. These configurations offer greater flexibility whilst maintaining the benefits of liquid ring technology in handling saturated or contaminated gases.
In addition, automation and Industry 4.Zero integration are permitting real-time diagnostics, fault detection, and far off operation, which are in particular beneficial in dispensed manufacturing environments.
Conclusion
The liquid ring vacuum pump sticks out as one of the most resilient and versatile vacuum technologies to be had nowadays. Its tested overall performance across a large number of industries speaks volumes about its adaptability and lengthy-time period value. From handling moist and corrosive gases to presenting strong vacuum in hard environments, it supplies a combination of reliability, low maintenance, and operational efficiency that few other structures can match.
While emerging technology provide exciting options, the liquid ring design stays essential in packages that require tolerance to infection, moisture, or temperature variations. By attractive with skilled vacuum manufacturers and integrating pumps with sensible gadget design, industries can retain to gain from this time-examined technology nicely into the future.
As the focus on energy conservation and environmental compliance intensifies, liquid ring vacuum pumps are poised to remain a vital component inside the worldwide business toolkit, evolving to satisfy the demanding situations of the next day without compromising on overall performance today.